Predictive Process Optimization
Nemak Trial: Zero Defect Production
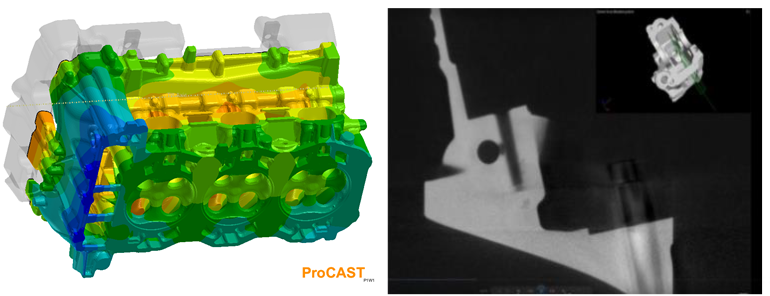
%
More coverage of datapoints
%
Increase in CAST process understanding
%
Increase in operator’s satisfaction
Data-Driven Digital Process Challenges
In the manufacturing industry, the imperative need to optimize the casting process as well as achieve zero defect products entails the requirement for reducing costs of production and increasing quality in casting and resulting parts. In such cases, hybrid simulation based data models that support the predictive diagnosis based on (historical) data analysis become essential.
Big Data Business Process Value
In the Nemak pilot a hybrid data simulation model was realized which uses real casting process data in order to improve the mathematical simulation model. Such a model is able to identify critical process parameters and their influence on the product quality. The hybrid simulation model enables the provision of an intelligent diagnostic solution which allows to continuously improve casting processes and help to predict critical defects in casting parts.
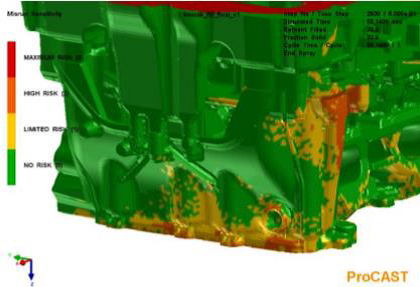
Large Scale Trial Performance Results
The Nemak trial has allowed the development of a simulation model of the casting process to predict miss run and porosity distribution based on the given specific defect predictors. Large 3D simulations have been performed and analyzed, and the study has shown that the model is able to indicate defects. Miss runs and porosity predictions gave a good agreement between the modelling results and experiences from the real process. In the final phase, an experiment of process parameters has been performed in order to identify optimal process parameter in order to reduce the production of defect parts and to improve the quality of the products.
Observations & Lessons Learned
Hybrid simulation models can enable an early identification of defects which leads to reduced costs and saved efforts. By examining modelling results, it is possible to identify process parameters that can be re-configured to significantly reduce the occurrence of production and quality problems.
The achievements have shown that combining process simulations and big data can improve and optimize overall casting processes and products. By investigating the simulation results corresponding to a large experiment of process parameters it is possible to identify the link between process parameters and defect creation.
Replication Potential
A mid-way change of the industry partner has enabled to test and analyze if parts of the outcomes are transferable. The majority of results were transferable in a reasonable time to the Nemak foundry which proofs that results of BOOST 4.0 are replicable to other companies in the casting domain in Europe or world-wide.
Nemak Linz GmbH
Linz | Austria
Pilot Partners
Standards used
-
Nemak internal ICT
-
Infrastructure Standards
Big Data Platforms & Tools
- ProCAST casting simulationBig
- Data Characterization
Data volume
20 GB per mould
Data velocity
2 GB per process per day
Number of sources
- CAD Data
- Casting process data
- Machine and process configurations
Open data
No
Implementation Assessment
Technical feasibility
The ESI casting simulation suite provides a generic hybrid simulation approach which can be adapted to individual customer needs. The technical feasibility of this approach was demonstrated in this pilot.
Economic feasibility
The developed solution can easily be replicated for similar casting processes (cyclic production with permanent mold processes). ESI offers customization projects in order to adapt the hybrid simulation approach for individual customers, which can then be used through a software leasing contract
Replication potential
The achievements of the BOOST project have shown that the methods and results of this business process are transferable in a reasonable time.