After sales service and downtime reduction
CRF autonomous assembly line factory 4.0
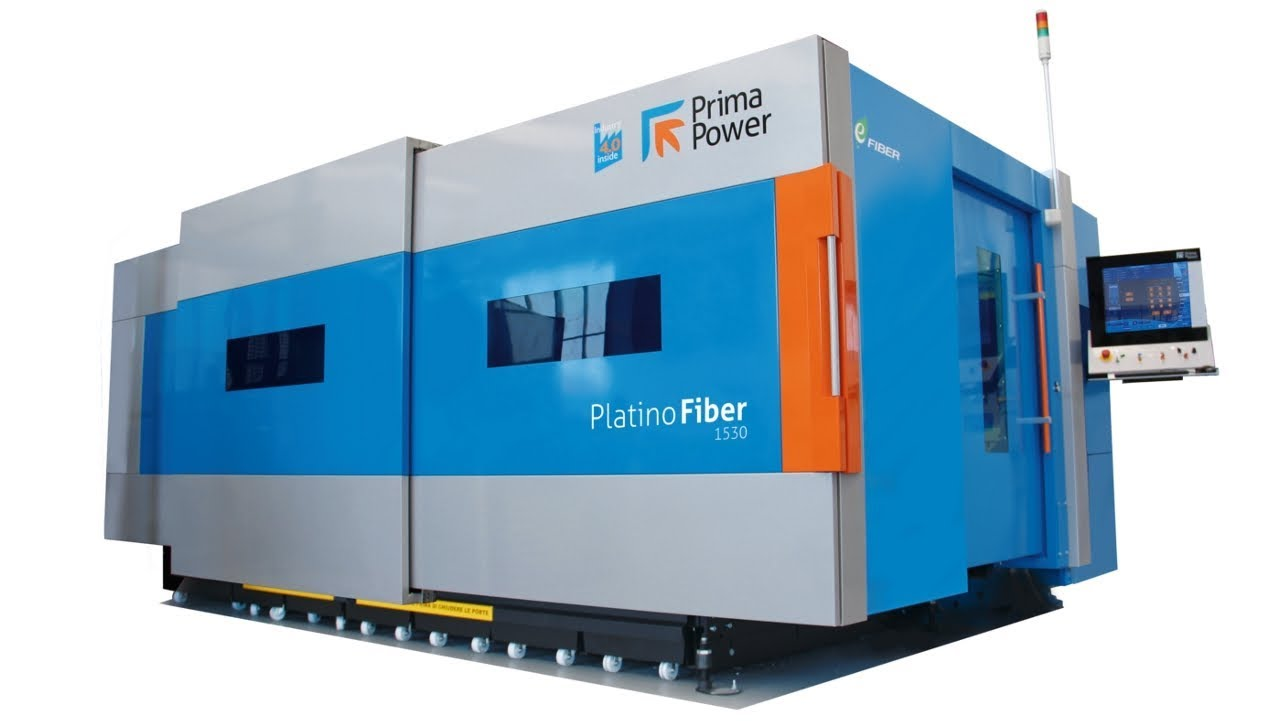
%
Increase in Customer Service Satisfaction
%
Increase in OEE level
%
Increase in Throughput (Job-Per-Hour)
Data-Driven Digital Process Challenges
The new business process is about the monitoring in real time of the laser cells. The key success factor is to be able to retrieve in real-time from the production systems the right data, at the right sampling rate and to be able to analyse it in order to provide a monitoring of the cell.
Big Data Business Process Value
Data coming from Prima Power Laser Machine: this laser machine was event-based, so it was not possible to have a classical data model, but with the new sensors implementation, PRIMA had the possibility to monitor and analyze different real time data parameters. Data were obtained from a MongoDB, uploaded to MindSphere and linked to the corresponding asset.
The software collects data and events coming from the Laser Machines and offers different ways of visualization and monitoring of the data.
It is a cloud application, running on the SIEMENS platform MindSphere. The app is linked to a MongoDB also instantiated into MindSphere. This MongoDB, in turn, collects information from other MongoDBs of Prima laser machines, instantiated on-board machine.
Data analysis and data visualization are implemented by means of diagrams and tables that allow monitoring and data insight of the events obtained from the Laser machines.
Large Scale Trial Performance Results
The new sensors and data acquired are:
- Camera systems monitoring
- Consumption Production Data
- Consumption Machine data
- Energy consumption (Powermeter)
- Gas consumption (Flowmeter)
The software collects data and events coming from the Laser Machines and offers different ways of visualization and monitoring of the data
This allows PRIMA to have a product quality monitoring of the laser machine and ready to provide a fast Service Support, in all those situations in which there is a machine downtime or deterioration in productivity due to the necessity of ordinary or extraordinary maintenance interventions.
Observations & Lessons Learned
As a countermeasure to the COVID-19 emergency situation and to mitigate the problem of the impossibility of physically attending the place where the machine is located, PRIMA organized a series of remote stations to simulate the laser systems activities and status for data generation and process simulation, in order to have a possible alternative useful for applications development and test.
A remote simulation was also carried out between a PRIMA laser machine and the CRF AGV fleet, trying to really reproduce what would happen in the production plant, through the exchange of production data between AGV and laser cell.
Replication Potential
This approach has been tested first of all on a Prima Power 2D cutting machine, but then could be easily transferred to all the Prima Power group machine, so for instance 3D cutting, welding, shaping and bending machine, but also on the new additive manufacturing machine.
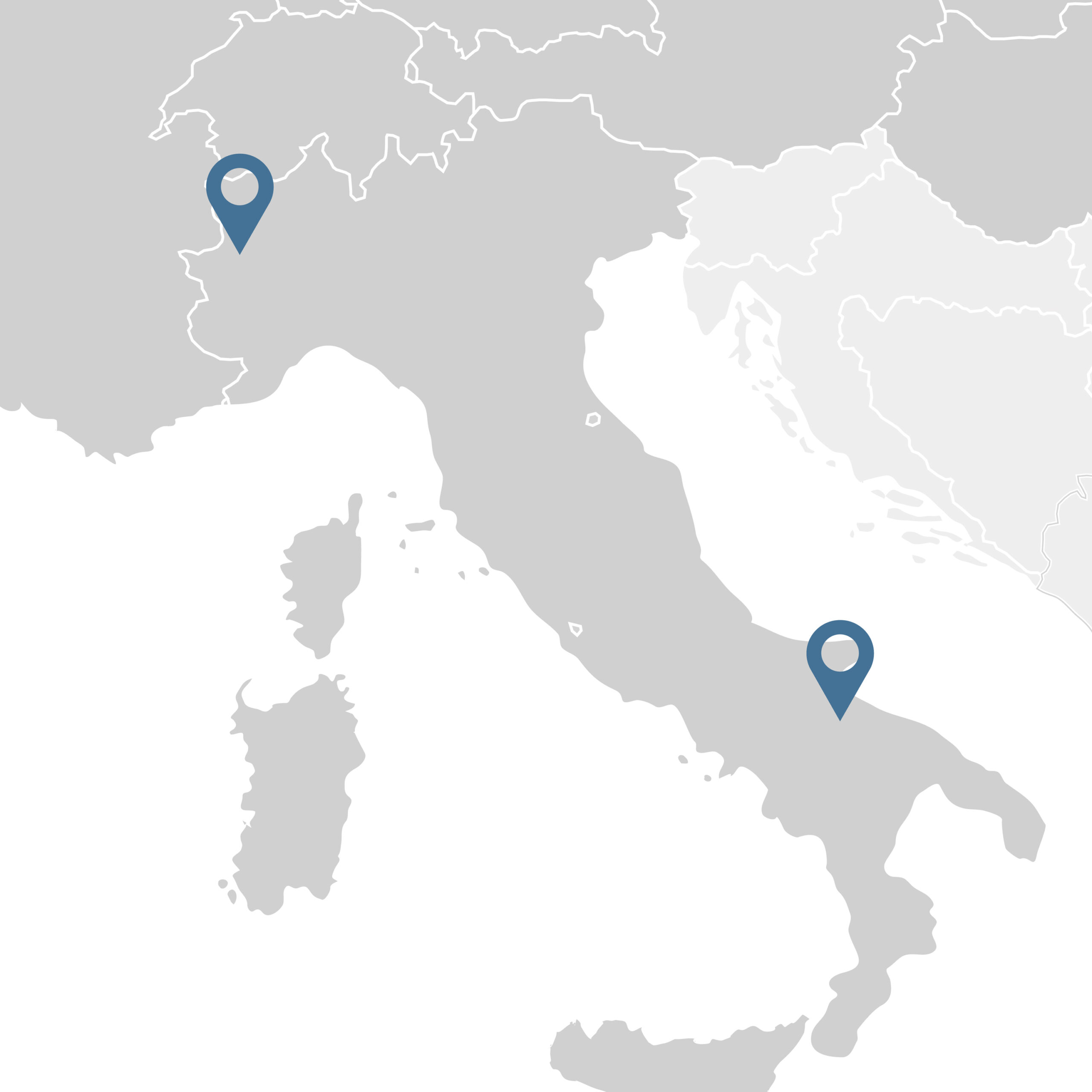
CRF Melfi Campus |Melfi, Italy
Prima Industrie Advanced Laser Centre | Collegno, Italy
Pilot Partners
Standards used
- International Data Spaces Association
Big Data Platforms & Tools
- Mindsphere
- Fiware
Big Data Characterization
Data Volume
300GB
Data Velocity
10 kB/s
Data types
-
Time series
-
Events
-
Alarms
-
Machine states
Number of sources
- Machine configuration
- Machine conditioning
- Operational data
- Production scheduling
- Component variants information
- Pilot area characteristics
Data data
No
Implementation Assessment
Technical feasibility
Economic feasibility
Replication potential