Analytics and anomaly detection
CRF autonomous assembly line factory 4.0
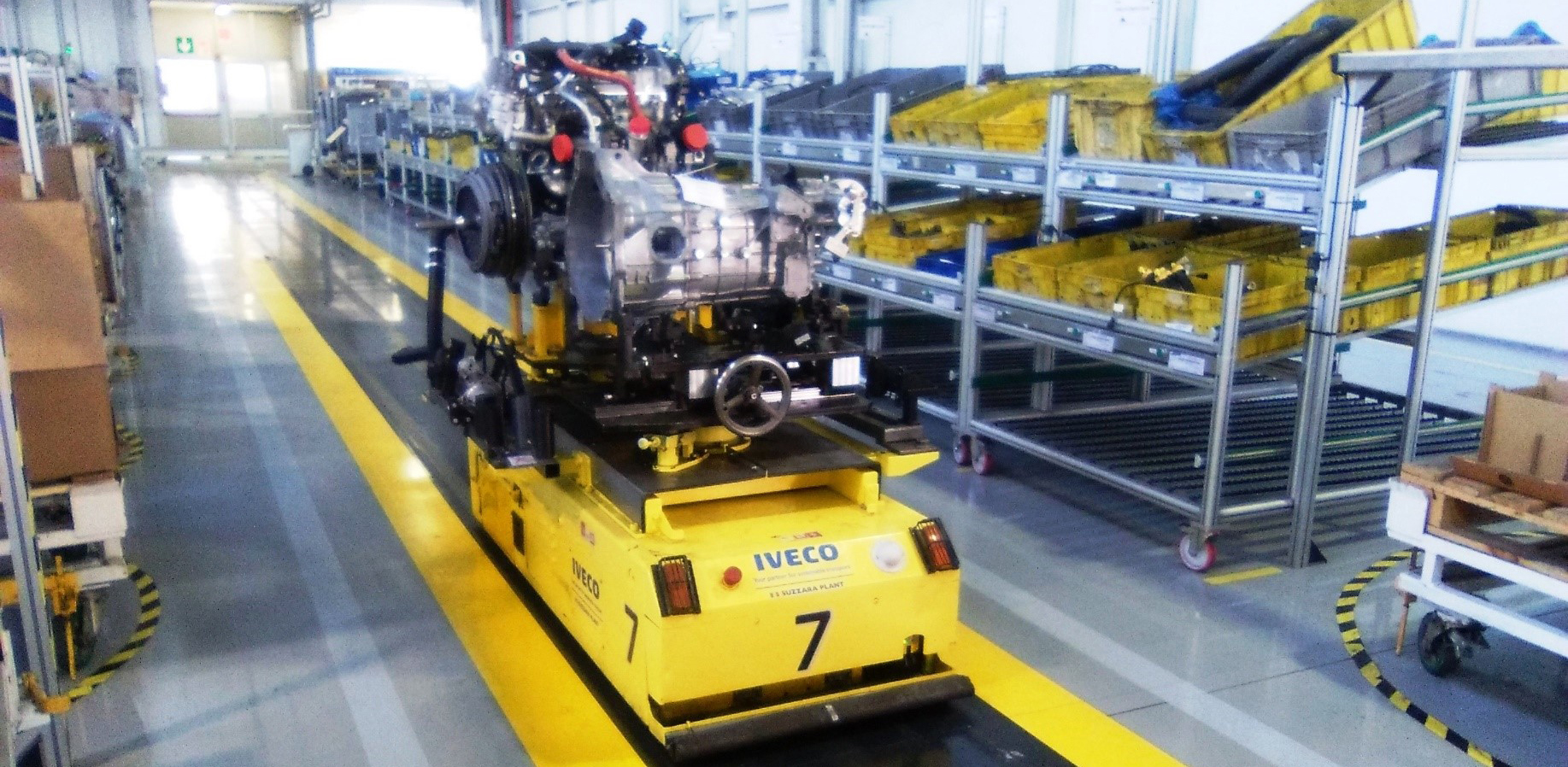
%
Saturation of AGVs
%
Reduction of maintenance cost
%
Increasing of the JPH (Job Per Hour)
%
Increase of the efficiency of AGVs
Data-Driven Digital Process Challenges
The pursuit of efficiency increase of the production actors is a subject of extremely high relevance in the manufacturing field, being one of the main factors which determine the overall system performance. In order obtain improvements, the effort is primarily concentrated on the understanding of the phenomena, often integrating the already available datasets with installation of different sensor systems, related to the operating conditions, so as to better the latter through the results coming from the development and application of suitable analysis instruments.
Big Data Business Process Value
The business process regards the monitoring and analysis of the working conditions of the mobile robots in order to improve their use, enabling the development of a maintenance schedule coming from a predictive analysis.
The first step of the process is represented by the retrieving of relevant data from the industrial environment with the correct characteristics (e.g. sampling frequency). The considered data typologies are three:
- Data from sensor systems (e.g. vibrational sensors) installed on relevant components of the mobile robots
- Data directly produced by the mobile robots during the execution of the production missions (e.g. battery level)
- Data coming from production management systems (e,g. mobile robots mission schedule)
Then, after their sending and appropriate storing in the pilot cloud platform (implementing suitable data models) is set-up, data are processed by a dedicated analysis application, developed inside the project, which has to produce, as main outcome, indications able to lead to an optimization of the mobile robots operating conditions.
In this way, it becomes possible to increase the availability and ensure the maximal saturation of the AGVs, reducing the amount of stops which are not related with the planned maintenance operations. This condition permits finally to optimize both the equipment investments and the maintenance cost.
Large Scale Trial Performance Results
Starting from the part of the business process related to the data gathering, the pilot development made possible to manage the huge amount of data produced by AGVs and industrial management systems which needed to be made available and then retrieved by the implemented infrastructure in order to be stored on the cloud. Then, another fundamental part has been the development of the analysis application, which had to be able to select and correctly process the relevant data. Finally, the sending of the results, using the developed data infrastructure, to the pilot industrial environment allows their implementation in the right management systems and so the subsequent use by the correct production actors/operators.
Observations & Lessons Learned
The most challenging aspect has been represented by the need to interface with heterogeneous devices in the industrial environment, which means dealing with specific communication protocol and different data acquisition speeds. Besides, it has been very important to align the information flow pace with that of the production process and the related data generation.
Replication Potential
The considered data process can be extended to other manufacturing applications taking into account the production actors characteristics, evaluating which are the necessary data for the analysis and so the need of further sensor systems, and the requirements in terms of data management and use of analysis results.
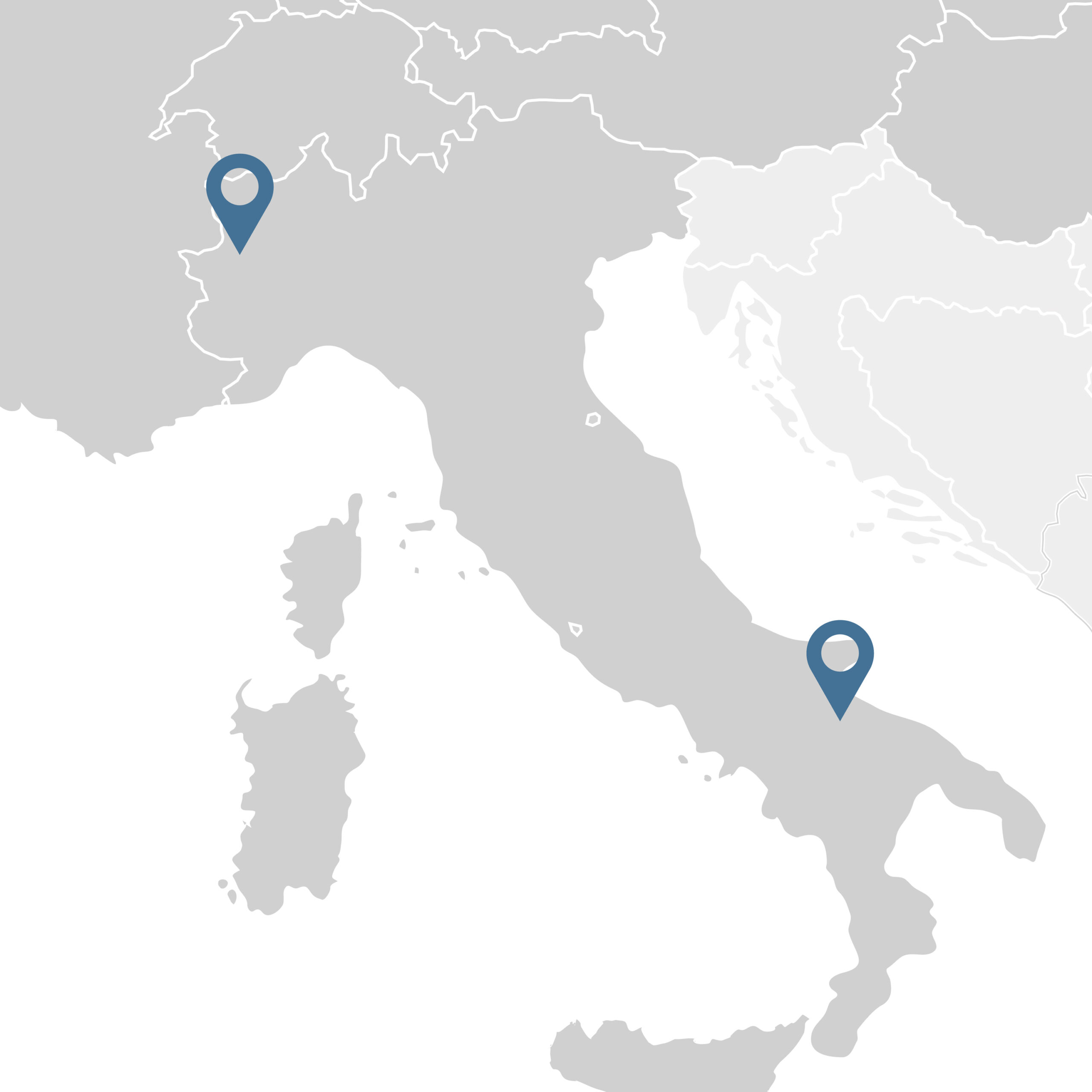
CRF Melfi Campus |Melfi, Italy
Prima Industrie Advanced Laser Centre | Collegno, Italy
Pilot Partners
Standards used
- International Data Spaces Association
Big Data Platforms & Tools
- Mindsphere
- Fiware
Big Data Characterization
Data Volume
300GB
Data Velocity
10 kB/s
Data types
-
Time series
-
Events
-
Alarms
-
Machine states
Number of sources
- Machine configuration
- Machine conditioning
- Operational data
- Production scheduling
- Component variants information
- Pilot area characteristics
Data data
No
Implementation Assessment
Technical feasibility
Economic feasibility
Replication potential