Vigilant 4.0
Autonomous In-line Quality Inspection Agent for Yield
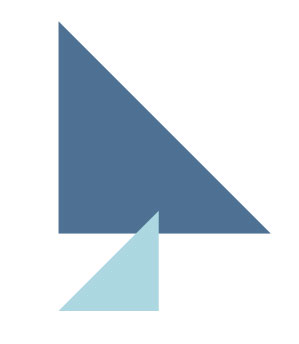
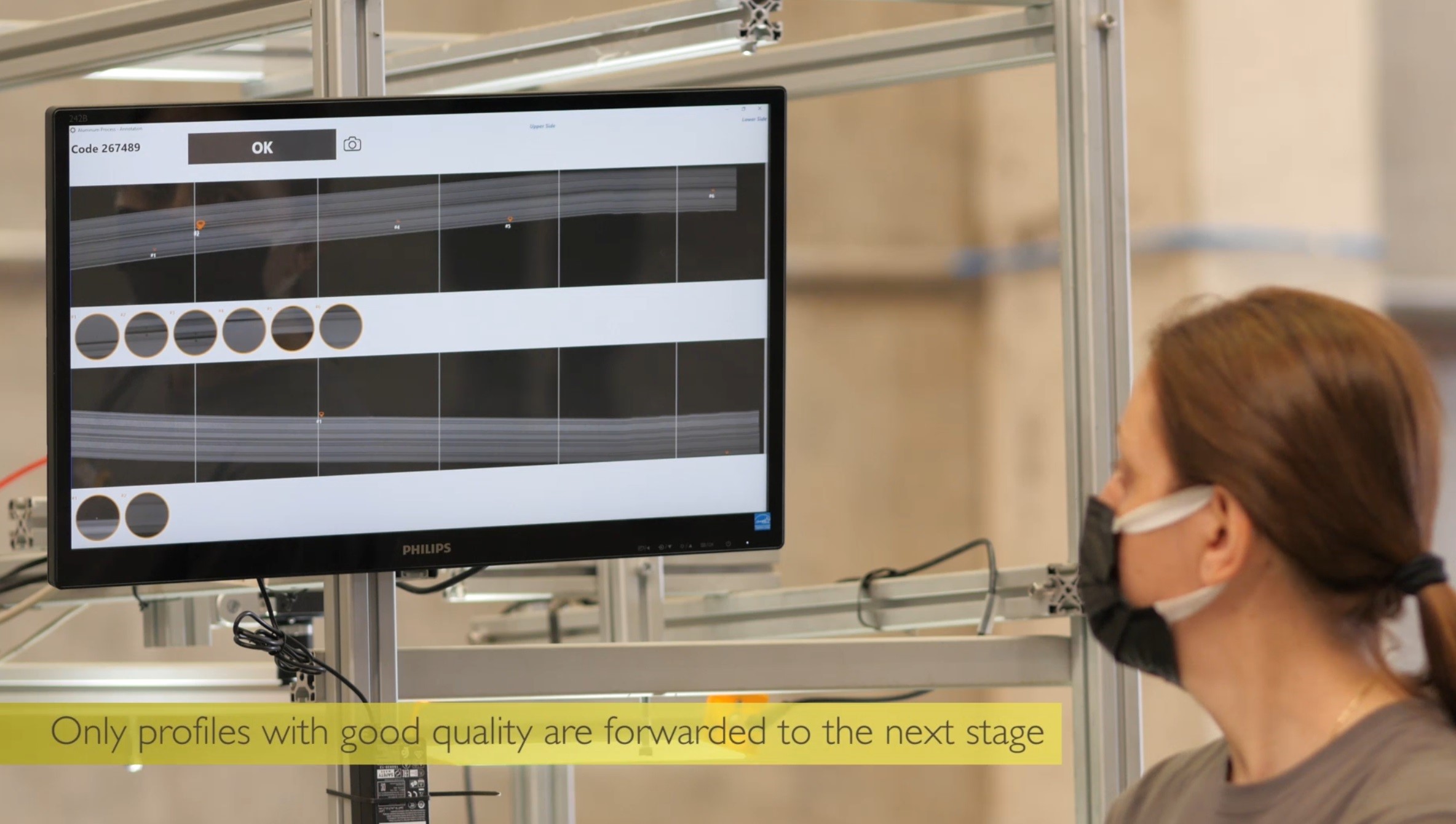
ALUMIL is the largest aluminium industry in Greece. The company has more than 30 years of history and 2.200 employees, in the design and production of architectural aluminium systems, and is one of the most advanced companies globally owning state-of-the art production lines in 12 factories located in 6 countries and 11 aluminium extrusion lines with a capacity of 100.000 tons.
Data-Driven Digital Process Challenges
The aluminium extrusion process is a complex process comprised of various stages: extruding, stretching, ageing, cutting, anodizing, powder coating etc. For quality assurance purposes, samples of the first few extrusions are taken for visual inspection. However, the speed of the production and the level of detail required to detect all types of non-conformities, make this process inefficient.
Big Data Business Process Value
The Vigilant 4.0 trial considers two main business processes for implementation:
Automated production orders: Vigilant 4.0 acts as a decision-making system, that performs automated profile sorting based on the quality of their surface. This procedure guarantees the reduction of scrap propagation in later production stages and the minimization of claims. On top of that, automated production orders are generated based on the number of the detected marketable profiles, allowing for time-to-market reduction.
Real-time/proactive identification of scrap generation: Vigilant 4.0 provides real-time / proactive identification of quality deterioration to initiate recommendations to the operators for in-time remedying and scrap reduction. To achieve that, production data and quality findings were analysed using the QARMA enabler and revealed unknown error sources and corelations that eventually led to increased productivity for the production lines.
Large Scale Trial Performance Results
The Vigilant 4.0 trial has allowed the development of an autonomous Quality Inspection Agent that is installed before and after the powder-coating process of an aluminium extrusion factory. It has achieved the prevention of scrap generation and scrap propagation, maximized the yield of the process and ensured the delivery of high-quality profiles in a timely manner. Vigilant 4.0 refers to an autonomous QA system, capable of making critical decisions based on the detected quality levels. It is installed in two key-points of the processing chain, before and after the powder-coating line, in order to optimize this resource intensive process of the secondary production.
The above have allowed the automated profile sorting with 97.5% accuracy, minimizing scrap propagation and claims/returns from the end customers. Moreover, the automated sorting decisions allowed the reduction of time-to-market by 18%. All in all, Vigilant 4.0 achieved an increase of yield by 30% and an energy reduction by 15%.
Value chain
Observations & Lessons Learned
Vigilant 4.0 discovered new ways to utilize production data and reveal unknown error sources, minimize time-to-market and eliminate claims.
During this trial, ALUMIL realized that automated profile sorting outperforms standard manual processes, also eliminating bottlenecks. Off-line data analysis revealed error sources and bad practices in production procedures that were responsible for scrap generation. In-time remedying can have a huge impact in production costs.
Production optimization depends significantly on production data, the availability of which can vary in different companies. Finally, workers gain gradually confidence to the system as they realize system’s performance and benefits.
Replication Potential
Vigilant 4.0 node can be installed as-is in any processing line of an extrusion factory (after extrusion, before and after powder coating). Moreover, during this trial, OPC-UA interfaces and protocols developed enabled the fast and easy integration with any system of the client (MES, ERP, PLC). Available production parameters may vary among companies, and a custom-made design for the optimization of the production may be required.
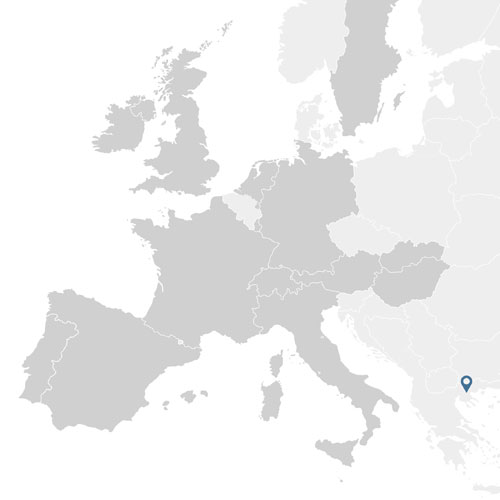
ALUMIL SA, Kilkis, Greece
Pilot Partners
Standards used
- OPC UA
Big Data Platforms & Tools
- D-Cube’s IoT Cloud platform
Big Data Characterization
Data Volume
500 GB
Data types
- Quality metadata
- Production parameters
- Sorting data
Number of sources
- Vigilant 4.0 compound sensor
- Machine parameters
- Manufacturing Execution System
Open data
No
Key Facts & KPIs
Productivity
PR1 – Increase of yield 30%
PR2 – Reduction of defective surface occurrence rate 49%
Speed
SP1 – Time-to-market reduction 18%
Sustainability
SU1 – Reduction of needs in energy resources 15%
Agility
AG1 – Accuracy of routing decisions 97.65%
AG2 – Reduction of claims 100%
Customization
CU1 – Industry 4.0 interfaces for easy integration with MES, ERP, machines YES
Adoption Assessment
Technical feasibility
Economic feasibility
Replication potential