Petrol-Chemical Pilot: Hybrid Circular Twins for Process Industry
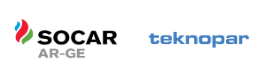
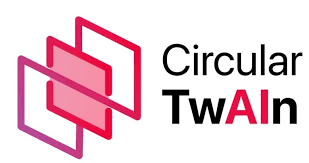
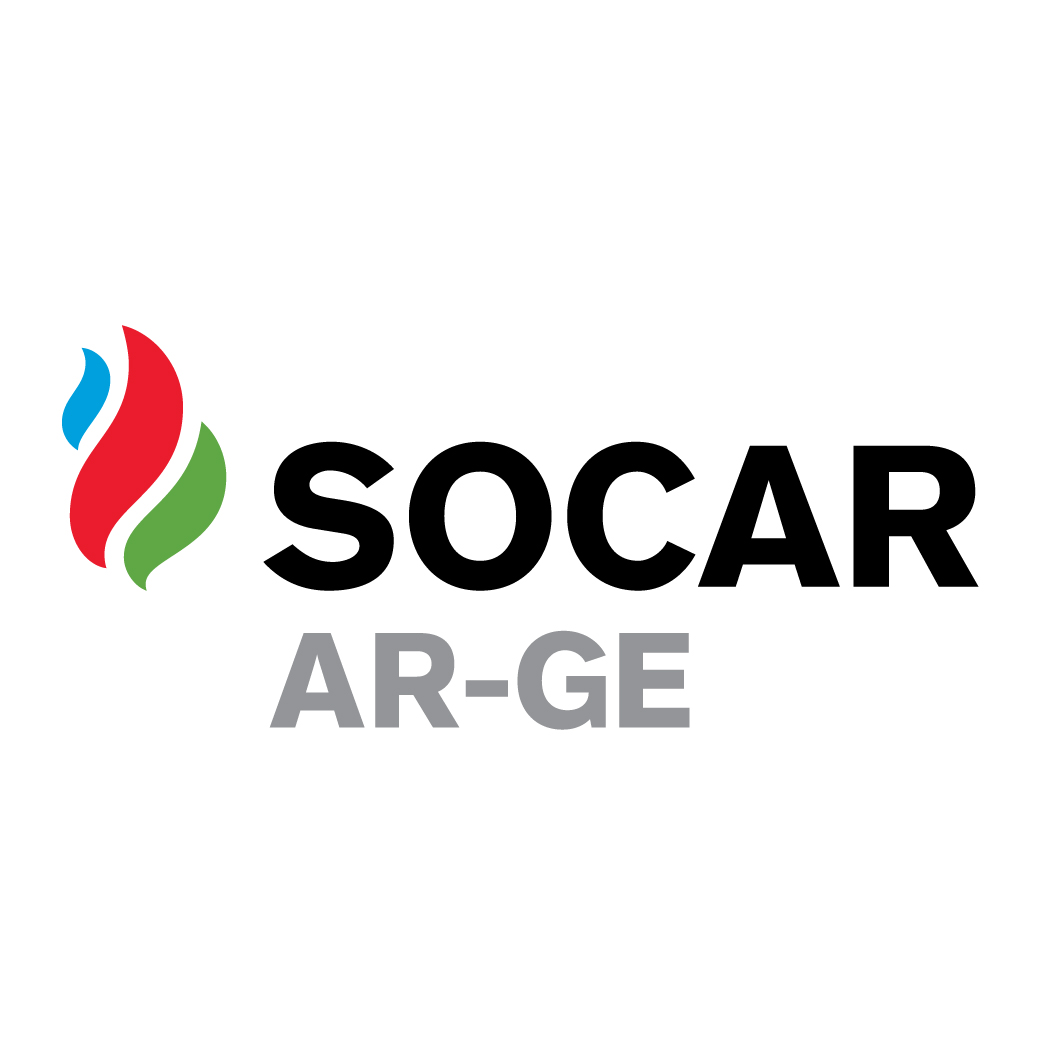
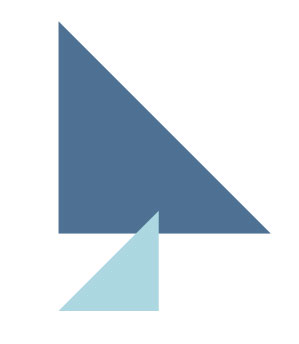
General Information
Challenge, Value & Description
Performance, Access & Contact
1 – General Information
Partners
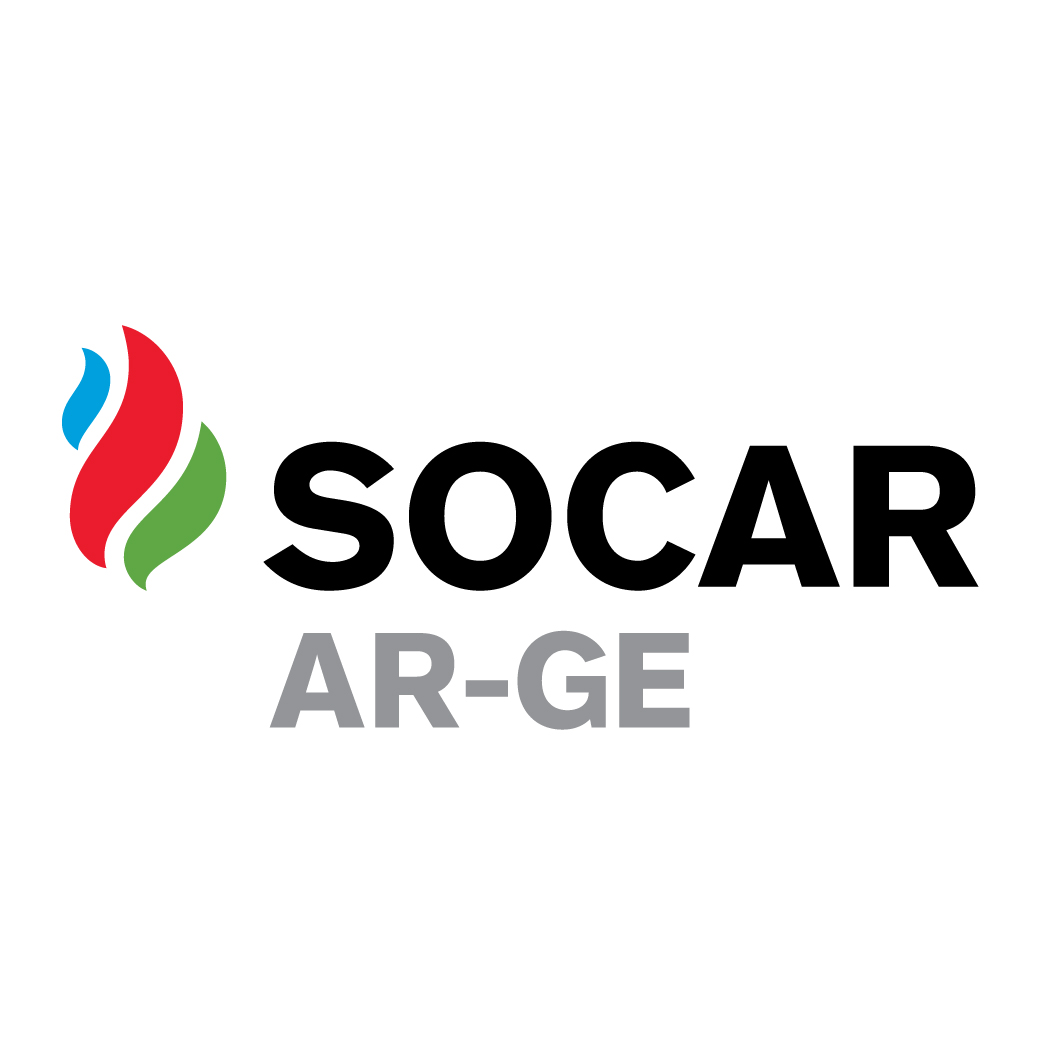
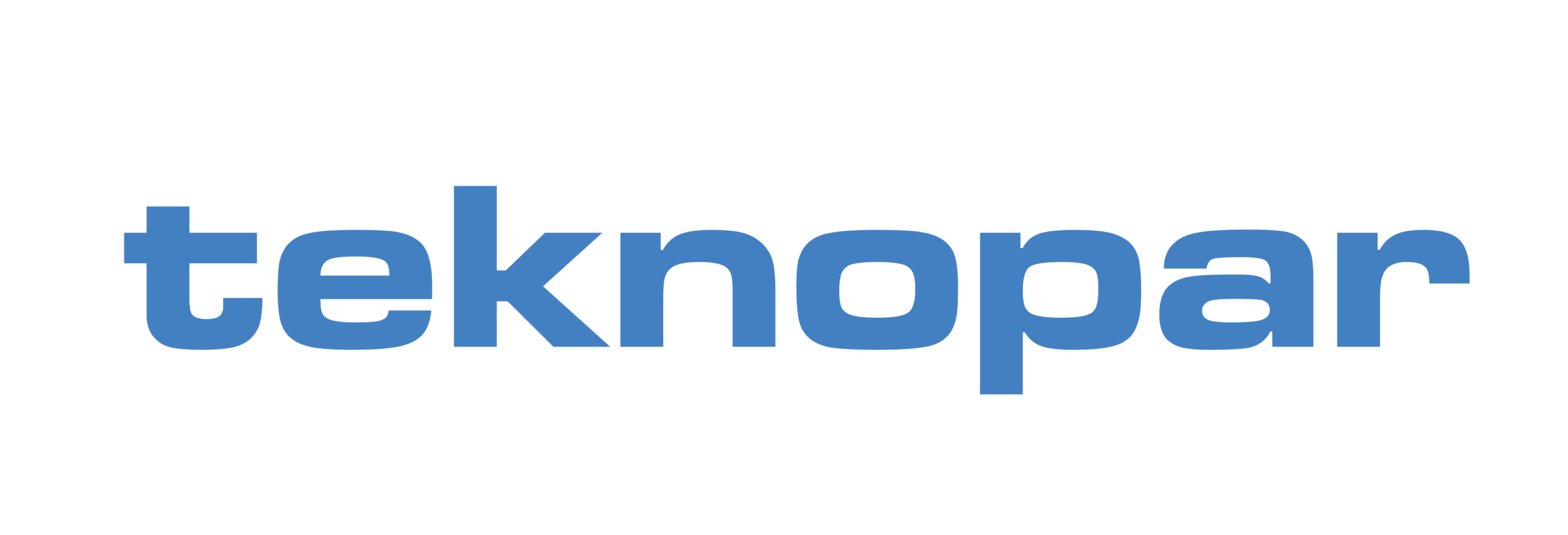
Sectors addressed
- environmental_green
- ict
- oil_gas
Application categories covered
https://www.circular-twain-project.eu/use-cases
Geographical Scope
- Europe
- Turkey & Caucasus (Georgia, Armenia, Azerbaijan)
Lifecycle level covered
Smart Maintenance
Customer Service
Circularity
2 – Challenge, Value & Description
Challenge
Before the PETRO Pilot, petrochemical operations faced significant inefficiencies and sustainability challenges. Manual monitoring of equipment and processes led to delayed responses to faults, increased downtime, and excessive energy consumption. Data was siloed across departments, limiting visibility and preventing predictive maintenance. Environmental compliance was reactive, with limited tools for tracking emissions or optimizing resource use. The lack of integration between operational data and decision-making systems hindered circular practices and innovation. These conditions posed risks to profitability, safety, and sustainability, highlighting the urgent need for digital transformation and intelligent process optimization.
Value
With the PETRO Pilot in place, petrochemical operations have become significantly more efficient, predictive, and sustainable. Real-time data from sensors and equipment is now integrated into a Digital Twin environment, enabling continuous monitoring, early fault detection, and predictive maintenance. AI models optimize energy use and reduce emissions, while the federated dataspace ensures secure data sharing across departments and partners. This transformation has led to reduced downtime, lower operational costs, improved regulatory compliance, and enhanced environmental performance—turning traditional linear processes into smarter, circular, and more resilient industrial systems.
Description
In the PETRO Pilot, the data exchange process is designed to enable real-time, intelligent, and secure collaboration across the petrochemical value chain. The process begins with sensor-equipped industrial equipment continuously collecting operational data—such as temperature, pressure, flow rates, and emissions. This data is streamed into a Digital Twin environment, which mirrors the physical processes and systems in a virtual space.
The plant operators and process engineers access this data through a federated dataspace, which ensures secure, role-based sharing across departments and external partners. AI models analyze the data to detect anomalies, predict equipment failures, and suggest process optimizations. These insights are shared with maintenance teams, who use them to schedule predictive interventions, reducing downtime and avoiding costly breakdowns.
Meanwhile, environmental compliance officers access emissions and resource usage data to monitor sustainability performance and ensure regulatory compliance. The dataspace also allows external auditors or regulators to view verified data snapshots, enhancing transparency and trust.
In cases where circular practices are applied—such as reusing by-products or optimizing energy loops—production planners and supply chain managers use the dataspace to coordinate with downstream partners, ensuring that recovered materials are reintegrated efficiently.
This integrated data exchange process transforms siloed operations into a connected, intelligent system, enabling safer, more efficient, and more sustainable petrochemical production.
Infraestructure Elements
- Private Cloud
3 – Performance, Access & Contact Info
Performance
In the PETRO Pilot, the Circular TwAIn project addressed long-standing inefficiencies and sustainability challenges in petrochemical operations by introducing a data-driven, AI-enhanced approach to process monitoring and optimization. Previously, operations relied heavily on manual inspections and siloed data systems, which led to delayed fault detection, unplanned downtime, and excessive energy consumption. Environmental monitoring was reactive, and circular practices were difficult to implement due to limited visibility into resource flows.
To overcome these issues, the pilot deployed Digital Twins of key equipment and processes, enabling real-time simulation and monitoring. These twins were fed by sensor data and integrated into a federated dataspace, allowing secure, role-based access to operational insights. AI models were applied to predict equipment failures, optimize energy usage, and reduce emissions. Maintenance teams received early alerts, while environmental officers gained access to continuous compliance data.
The transformation resulted in:
- Reduced downtime and maintenance costs
- Improved energy efficiency and lower emissions
- Enhanced regulatory compliance
- Greater operational transparency and collaboration
- Support for circular resource flows within the plant
Overall, the PETRO Pilot demonstrated how digitalization and intelligent data exchange can make petrochemical production safer, more efficient, and more sustainable.
Lessons Learned & Observations
The PETRO Pilot provided valuable insights into the digital transformation of complex industrial environments. One of the most important lessons learned was the critical role of real-time data integration. Prior to the pilot, data was often siloed across departments, limiting visibility and slowing down response times. By implementing a Digital Twin and federated dataspace, the pilot demonstrated how centralized, real-time access to operational data can significantly improve decision-making and responsiveness.
Another key takeaway was the importance of predictive maintenance. AI models trained on historical and live sensor data enabled early detection of equipment anomalies, reducing unplanned downtime and maintenance costs. This shift from reactive to predictive operations proved to be both technically feasible and economically beneficial.
The pilot also highlighted the value of cross-functional collaboration. Engineers, maintenance teams, and environmental officers were able to work more effectively thanks to shared access to relevant data. This not only improved operational efficiency but also supported compliance with environmental regulations by enabling continuous monitoring of emissions and resource use.
Finally, the PETRO Pilot confirmed that digitalization can support circularity even in traditionally linear sectors. By optimizing resource flows and enabling the reuse of by-products, the pilot opened new pathways for sustainability in petrochemical production.
Replication Potential & Feasibility Assessment
The PETRO Pilot has demonstrated a high potential for replication across the petrochemical industry and other process-intensive sectors. Its architecture—based on Digital Twins, AI-driven analytics, and a federated dataspace—can be adapted to various plant configurations and operational scales. Because it leverages open standards and modular components, the solution is technically flexible and can integrate with existing industrial systems, including legacy infrastructure.
From a technical feasibility standpoint, the pilot has proven that real-time data integration, predictive maintenance, and emissions monitoring can be reliably implemented using commercially available technologies. The use of a Digital Twin allows for scalable deployment, from individual equipment units to entire production lines.
In terms of economic feasibility, the pilot has shown that the initial investment in sensors, AI models, and data infrastructure can be offset by significant cost savings. These include reduced downtime, lower maintenance costs, improved energy efficiency, and better compliance with environmental regulations. The ability to optimize resource use and reduce waste also opens new opportunities for circular business models, such as by-product valorization or energy loop reuse.
In conclusion, the PETRO Pilot offers a replicable, cost-effective, and future-proof model for digital transformation in the petrochemical sector—one that enhances operational resilience while supporting sustainability goals.