Teknopar
SMART-CNC
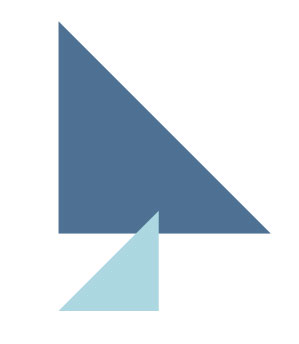
Teknopar is an R&D performing SME, founded in 1996 and based in Ankara, and it is one of the leading providers of automation systems and solutions in Turkey for industrial facilities, energy, mobility, and defence sectors.
Developing technologies are closely monitored and the latest developments are included in our industrial applications, and industrial projects that are developed and implemented are planned to meet the requirements at the highest level both economically and technically. By combining information technologies with control, IoT, sensors, automation, robotics, and operational technologies, TEKNOPAR develops digital twins, industrial communication systems, servo-controlled motion systems, embedded software, industrial software and data processing platforms.
Process Challenges
The challenges in this project were continuously acquiring data on a production environment, gathering data from CNC machines, sensor selection such that production is not interfered with, and obtaining tool wear parameter with It is not an easy process to estimate tool wear and to calculate remaining useful life (RUL). The least invasive sensors that could be used for tool wear estimation purposes are selected and the most fitting data transfer protocols are selected. PLCs that were projected for the use in the proposal of the project were not used since they are not able to sample 24-bit resolution data with high sampling frequency. A driver was developed to be able to gather data from FANUC’s CNC controllers. Certain changes on the configurations on the CNC machines were made to be able to acquire controller data.
Process Value
The SMART-CNC project develops a cognitive digital twin used to reinforce OEE optimization (OEE= (Availibility) x (Productivity) x (Quality)) and RUL estimation of the CNC machines. The developed outputs (cognitive digital twinbased RUL and cognitive digital twin based OEE) is a new pilot environment where the CNC machines are used to manufacture metal goods. Manufacturing parameters (input and output parameters), as well as machine status data, that is gathered from the CNC machine and by the installed sensors/sources (vibration, current, sound, shaft speed, mileage power, energy consumption, etc.) are compiled to monitor the real-time status of the CNC machine and production. The digital twin developed in the project presents 3D visualization of the machine and graphical representation of the collected data in real-time. That way, tool wear on the CNC machines are predicted and OEE is optimized.
Experiment Performance
The SMART-CNC experiment has allowed the use of advanced ML/DL algorithms for the estimation of tool wear. Data from FANUC controller and dynamic sensors have been visualized on a digital twin platform. This platform acquires data from InfluxDB and does data visualization using Grafana. The 3D model of CNC machines and sensor locations/values were made available on the 3D model. In the Digital Twin UI, the G-Code, several sensor values that are available within the machine such as temperature, position, load, power, feed rate have been visualized, the changes on these values can be seen in real-time. The errors and reasons that the machine is stopped can be seen from the digital twin screen. The operating minute counter and milling second counter is useful in calculating OEE. Thanks to the Digital Twin model, the business owner is able to monitor their CNC machines anywhere, at any time. The changing of the tool is monitored using GCode and tool number value also operators logs. That way, the useful lifetime of a tool is calculated for the ML/DL model. Dynamic sensors that are used in this experiment (Accelerometer & Microphone) allowed for accurate/early detection of tool wear. An F1 Score of 0.96 was achieved on the tool wear problem.
Value chain
Observations & Lessons learnt
Sampling rate of PLCs were insufficient for dynamic sensors such as microphones and accelerometers. Resolution must also be considered when trying to receive data from PLCs at high frequency. So, DAQ systems were used rather than PLCs.
The DAQ used had 50 kHz sampling rate and 24 bits resolution, which was more than enough to obtain the harmonics produced by the tool and the spindle motor.
To obtain data from FANUC controllers, a library that is not open source must be used. To address this problem, a library was developed that is able to gather data from CNC machines
and send the data through MQTT/InfluxDB protocols.
The port 8193 on the CNC Machines must be open to gather the data from Ethernet cables. Certain configurations on the machine were made to be able to gather data from the
controller continuously.
Replication Potential
A factory owner could replicate SMART- results with acquiring a high sampling rate and high precision Data Acquisition System and dynamic sensors such as accelerometers, force sensors, acoustic emission sensors and microphones.
The selection/installation of these sensors however requires expert knowledge.
Acquiring data from the CNC controller and sending that data to a database is a hefty process that relies on software knowledge. Replication of the FANUC driver requires lots of time/effort. Although it consists of open source components, it is not easy to build the digital twin for visualization, and to train the AI models.
Pilot Partners
Standards used
- TCP/IP
- REST API
- ISO20140-5
- ISA95
- IEC61804
- ISO27001
Digital Platforms & Tools
- InfluxDB 2.0
- LabView
- Fanuc Driver
- Grafana
- Tensorflow
- Python
Big Data Characterization
Data types
- Telemetry data
- Production data
- Statistical data
- Dynamic data
Number of sources
- Data fron the CNC controller
- Data from dynamic sensors
- Machine configuration
- Operational data
Open data
No
Key Facts & KPIs
Productivity
PR1 – OEE increase 25%
PR2 – Productivity increase 15%
PR3 – Quality cost reduction 50%
Speed
SP1 – Programming time reduction 90%
SP2 – Data Collection platform latency 100 ms
Sustainability
SU1 – Process efficiency 95%
SU2 – Waste reduction 20%
Agility
AG1 – Inventory reduction 20%
Customization
CU1 – RUL Estimation F1 Score 96%
Adoption Assessment
Technical feasibility
Economic feasibility
Replication potential