Remaining Useful Life (RUL) at DANOBAT
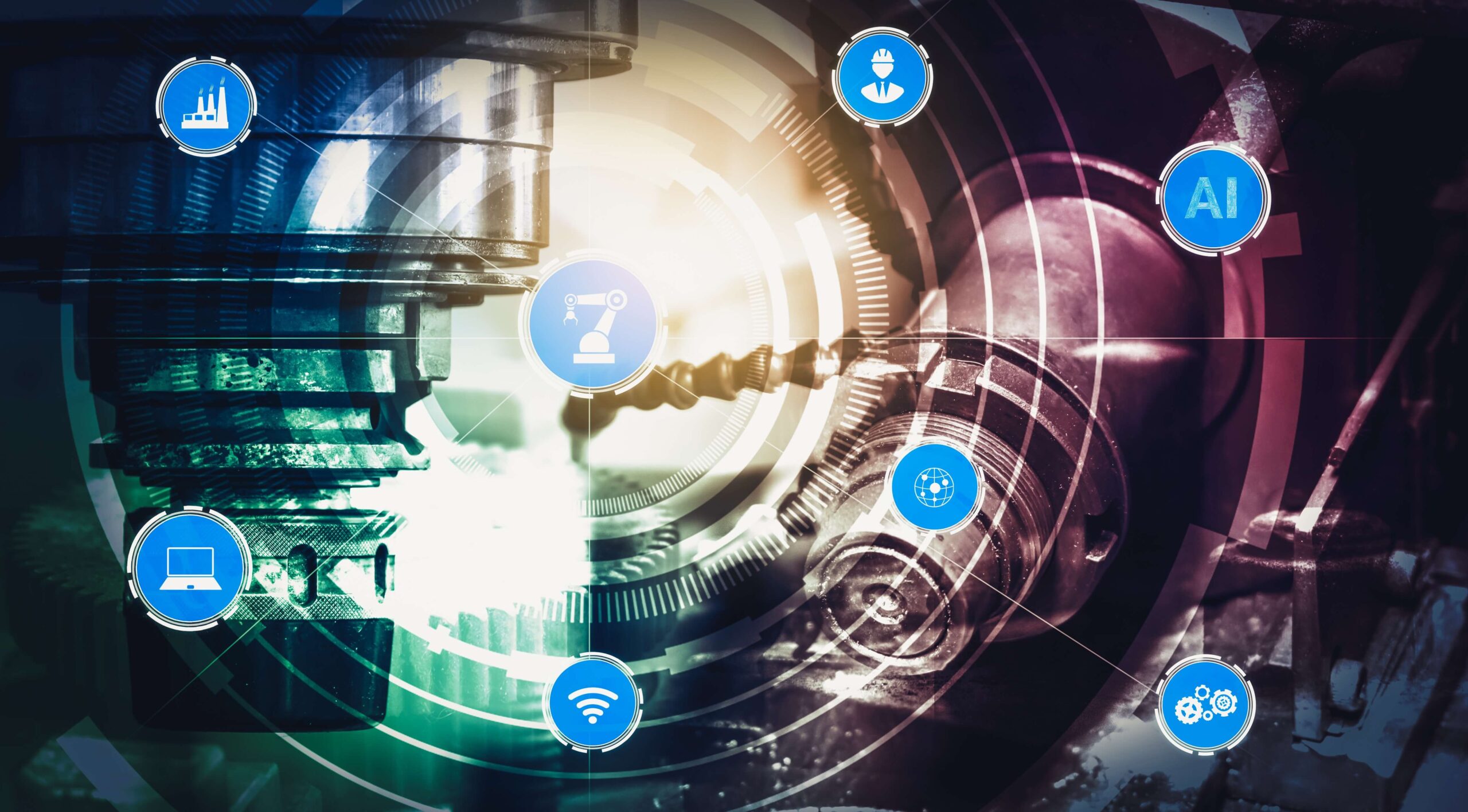
ATLANTIS Engineering and DANOBAT Corporation are working together in one of the pilot cases of the QU4LITY project. The focus is on the griding machines of DANOBAT, the manufacturer, which are critical because they handle high value material. The manufacturer has acknowledged that Zero Defect Manufacturing (ZDM) is key to address challenges related with the digitization and globalization of industrial manufacturing. To serve this scope, the technology provider ATLANTIS followed a methodology to estimate the Remaining Useful Life (RUL) of grinding machines, taking advantage of a mix of sensor measurements, such as engine intensity, load, position, power, speed and temperature. The findings were published at the 30th Flexible Automation and Intelligent Manufacturing (FAIM) Conference, which was planned for 2020, but because of the pandemic it was postponed for 2021.
The article was published in 2020 in a special issue of Procedia Manufacturing as an open access article under the CC BY-NC-ND license and was presented on the 9th of September 2021 at the online FAIM Conference. It is available for free download https://www.sciencedirect.com/journal/procedia-manufacturing/vol/51?page=3. FAIM brought together 371 papers published, 40 countries represented, 225 reviewers, 48 members of the Scientific Committee and on average about 250 registered participants for each of the four days of the Conference.
The outcome of the work from ATLANTIS and DANOBAT has shown that the RUL analysis can provide valuable information for the deterioration rate of assets, which is defined as the length from the current time to the end of the useful life. The paper presented the applied methodology, which capitalised on the Long Short-Term Memory (LSTM) Neural Network algorithm.
The monitoring system has been exploited, in order to analyse the collected data to deduct conclusions about the status of the equipment. The Remaining Useful Life approach was used to better understand the process and predict the time until the operation status falls outside desired specifications. The estimation of the RUL of critical components of the machine enables an informed planning of repair activities that minimises the impact on productivity and avoids quality issues for the manufacturing plant.