Optimizing Solder Paste Inspection
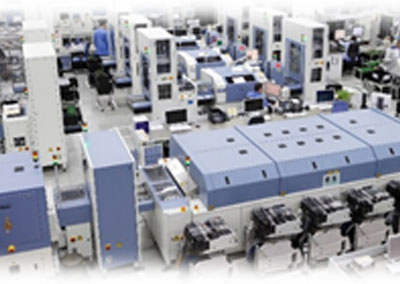
To strive for Zero Defect Manufacturing a decision support system based on inspection data and Machine Learning techniques has been developed.
Rising product complexity, customer requirements and global competition developed high product quality as a major competitive advantage. Customer demands of high quality standards force manufacturing companies to improve their products and processes constantly. As a result, no defects should remain undetected. This leads to inspection systems that are highly sensitive to variations in product characteristics. Thus, the economically optimal adjustment of the inspection severity leads to high pseudo defect rates. To reduce pseudo defect rates companies use process experts to verify manually the automatically generated inspection results for parts that had been declared as defective. This set up however, leads to additional inspection time and costs, and to some degree of uncertainty due to human error and variability in expertise. Therefore, the development of reliable support systems has become of great interest from an economical point of view.
As data driven approaches have proved to be very efficient for this matter, Machine Learning (ML) techniques were used to build a decision support system for industrial quality inspection processes. In the field of ML there is an increasing variety of methods and algorithms that can be used for all kinds of learning tasks. However, supervised and unsupervised learning, are the most used learning tasks in this field. Supervised learning requires the existence of a well-defined target variable. If this target is e.g. not available, unsupervised learning can be used to identify yet unknown structures and patterns (e.g. clusters or outliers).
The decision support system method proposed consists of two sub-methods. The first one is based on a One-Class Support Vector Machine (OCSVM) to detect outliers on the whole data set. For the second sub-module Decision Trees (DTs) were selected because these models are highly interpretable.
The developed decision support system was applied within a Solder Paste Inspection (SPI) process in surface mount technology (SMT) assembly in the Siemens Lighthouse Factory Amberg. SPI measures automatically the solder paste position and geometry on printed circuit boards (PCBs). The evaluation of the measured values with the corresponding specifications is fully automated, whereby operators have to manually double check as defect declared pads.
By applying the developed decision support system to the considered Use Case 99.91% of the predicted labels comply with the expert assessment. Therefore, it can be concluded that the SPI verification result can be received by using the proposed method which evaluates the recorded measurements in a multivariate way.
However, further research questions arose during the development of this decision support system:
- Examination of specific defect patterns instead of the binary defect / no defect classification
- Taking other data sources (e.g. image data) into account
- Evaluation of further supervised and unsupervised learning techniques for a broader variety of applications
Further information regarding the presented decision support system can be found in:
Schulte, Lukas; Schmitt, Jacqueline; Meierhofer, Florian; Deuse, Jochen (2020): Optimizing Inspection Process Severity by Machine Learning under Label Uncertainty. In: Isabel L. Nunes (Hg.): Advances in Human Factors and Systems Interaction. Proceedings of the AHFE 2020 Virtual Conference on Human Factors and Systems Interaction. International Conference on Applied Human Factors and Ergonomics (AHFE). USA (Virtual Conference), 16. – 20.07.2020. Cham, Switzerland: Springer.