OMETRI
NUEVA HERRAMIENTA DE CORTE, S.A
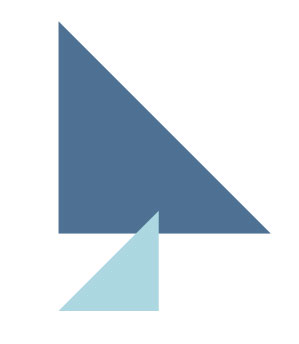
Nueva Herramienta de Corte (NECO) is a tool manufacturer which possesses an experience of over 75 years in the design, manufacturing and marketing of precision cutting tools and cylindrical and flat rolling dies. NECO is integrated into the structure of Tivoly Group, and currently, the plant of NECO in Elorrio has become the focal point of the group for the design most important products are taps, drill bits, end mills, reamers, cylindrical and flat rolling dies and other special tools. Based on the exercise of leadership and guided by a market adapted Strategic Plan, NECO is driven by the satisfaction of its customers, counting with the participation of all the people.
50% of the NECO net sales take place in foreign markets, with a presence in over 40 countries worldwide. The orientation towards the customer is reflected in its organization into divisions aimed at different markets to which they target their products and services. To provide greater responsiveness to changing market needs, the business units are organized into multidisciplinary teams. NECO has significant resources, both human and material, oriented to the innovation of its products and services. NECO conducts joint development projects with technology centres, devoting to them a 2% of its sales budget
Process Challenges
The high-speed steel tap production process is a complex process comprised of various stages: starting from steel bars we need cut the material, outside diameter & square grinding, flute, thread and chamfer grinding and the last step of the process which is the customisation of the taps, starting from degreasing, cleaning and coating of the products. For quality assurance purposes, NECO has always measured the products mainly manually without a standard automatized process.
Hence, there was not a quality procedure stablished on the manufacturing lines, making the tap production process inefficient and the detection of quality defects and non-conformities was done manually and randomly, making the production process inefficient.
Process Value
The implementation of OMETRI pilot in NECO´s manufacturing process implied that the business process was modified, and the digitization on the production process was done, integrating some digital components on it.
The major development of the experiment consisted on using an optical measurement machine to measure the cuttingedge form of the taps. The results from this device were used to feed the Remaining Useful Life (RUL) enabler in order to correlate the machine parameters with the quality of the cutting edge of the tools.
With this improvement, NECO has reinforced the following strategies: a) Detection: by improving the quality inspection processes, automated it and providing real-time up-to-date information of the quality of the products, b) Prediction and prevention: by establishing correlations among a number of variables and adjusting the parameters for this operation
accordingly to the increased knowledge obtained from the algorithms by the ATLANTIS enabler. Finally, it must be highlighted that improvements through Autonomous Quality enables NECO to provide with high quality products to its clients under lower production costs.
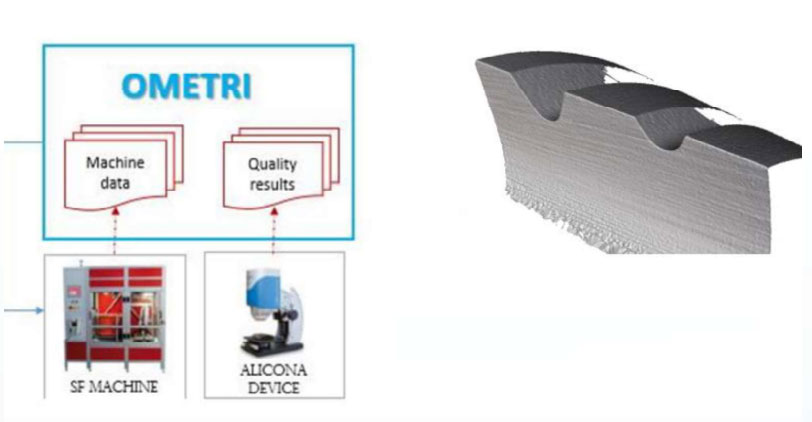
Experiment Performance
The objective for NECO in this experiment was to develop a Zero-Defect Manufacturing framework to improve a finishing operation the company has.
With this operation, the cutting edges of taps are improved, providing a proper shape for the coating operation with ceramic materials, and an enhanced performance in operation.
The key part for this strategy was to establish solid Detection and Prediction and Prevention strategies. On the one hand, the dimensions of the tap were accurately measured in order to identify defects in the cutting edge; On the other hand, a correlation among variables were established, which are critical in the operation, in order to optimise the process and the performance of the abrasive media in order to provide shape to those tap cutting edges.
With this experiment, a more repeatable and consistently performing tap manufacturing operation has been achieved, with 100% correct taps produced in the operation thanks to the improvements in automation regarding the measurement process. Moreover, tolerances have been implemented, ensuring higher-quality products and reinforcing NECO´s strategy towards continuous improvement on its production process.
Value chain
Observations & Lessons learnt
Knowledge improvement about different areas of knowledge:
- Qu4lity´s architecture.
- ATLANTIS device´s structure and capabilities.
- Analysis of the cutting-edge prep process parameters of the taps themselves and the potential for quality results of the taps for the early detection of abrasive deterioration.
- Behaviour of the last step of the tap manufacturing process and its influence on performance of the tap
- Now every machine high performance tap is measured and storage for future analyses, data measurements and storage.
- NECO has taken advantage of having a non-destructive methos for the quality inspection of the products and it has stablished a quality process based on its continuous improvement strategy.
- Improvements through Autonomous Quality enables NECO to provide with high quality products to its clients under lower production costs.
Replication Potential
NECO has integrated the digitalization in its manufacturing lines and this quality improvement provides transversality to the tap production process. Moreover, NECO and ATLANTIS are already collaborating, sharing information on data source formats and structure to be analyz particularities. NECO, meets the requirements of Qu4lity for the manufacture of taps, positioning in the market as a Digital Factory provider validated by Qu4lity Marketplace and autonomous QU4LITY concept enhancing their strategy to achieve ZERO-DEFECT-MANUFACTURING.
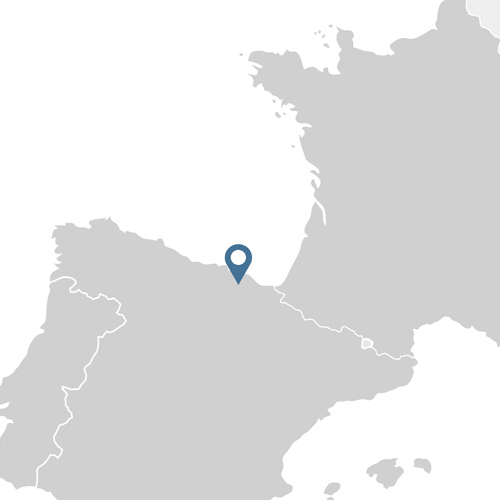
NECO, Elorrio
Pilot Partners
Standards used
- Qu4lity´s architecture
Digital Platforms & Tools
- ATLANTIS
- ALICONA
- STREAM FINISHING MACHINE
Big Data Characterization
Data types
- Quality metadata
- Production parameters
- Sorting data
Number of sources
- ALICONA device
- ATLANTIS platform
- Algorithms
- STREAM FINISHING
- MACHINE
- QU4LITY´s architecture
Open data
No
Key Facts & KPIs
Productivity
PR1 Digitization of the tap´s measurements 60%
PR2 Reduction of defective taps produced 100%
Speed
SP1 Time to market reduction 10%
Sustainability
SU1 Cost savings at the Tribofinition stage 15%
Agility
AG1 Reduction of claims 100%
Customization
CU1 Industry 4.0 interfaces for easy integration with ERP, machines YES
Adoption Assessment
Technical feasibility
Economic feasibility
Replication potential