KOLEKTOR
Autonomous detection and removal of defects in injection moulding
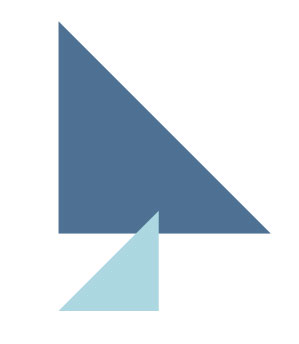
Kolektor Mobility is a multinational company with over 50-year-long tradition in production of components and systems for automotive industry. The whole group together with technologies and construction division employs over 5300 people worldwide and has turnover of € 900 million. In Slovenia, it counts among most successful industrial companies.
Kolektor Mobility is a renowned pre-development supplier for numerous globally leading manufacturers in the automotive arena (BMW, Renault, Bosch, Continental, Brose, etc). Basic business fields are systems and components mainly for the automotive, further divided into programs: commutators, hybrid parts, electronics and drives, and the magnets. Kolektor has built its competence based on own machine building and introduction of modern ICT solutions into production. Our technology excellence is proven by innovation with 50 international patents.
Process Challenges
Injection moulding is widely used manufacturing process for producing parts by injecting molten material into a mould. Parts to be injection moulded must be very carefully designed to facilitate the moulding process; the material used for the part, the desired shape and features of the part, the material of the mould, and the properties of the moulding machine must all be considered.
Anomalies anywhere during the moulding process may degrade the quality of moulded parts. Without real-time information about the production process, it is also impossible to correct and optimize the process. The challenges are better understanding the moulding process, and real-time detection and possibly prediction of failures.
Process Value
Injection moulding is widely used for manufacturing a variety of parts, operating also in harsh environment. Injection moulding can be performed with different materials such as elastomers, thermoplastic, and thermosetting polymers. Digitalization of the various stages of the injection moulding process is crucial step in the optimization of the whole manufacturing process. To reduce the occurrence of errors in the production and to optimize the production, the IT/OT digital infrastructure is a first step in the autonomous quality control. It enables real-time information about the production process and enables data acquisition for cognitive models. Deployment of advanced cognitive models to monitor the injection moulding process and to control the quality of the produced parts is the next step towards the zero-defect manufacturing.
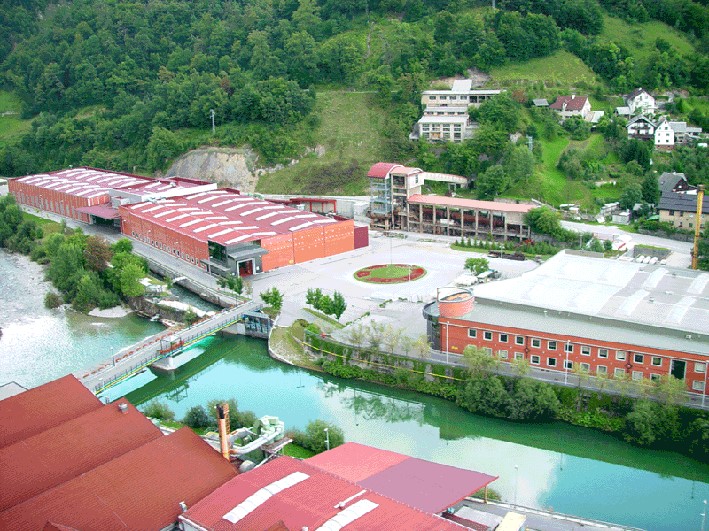
Kolektor seat in Idrija, Slovenia
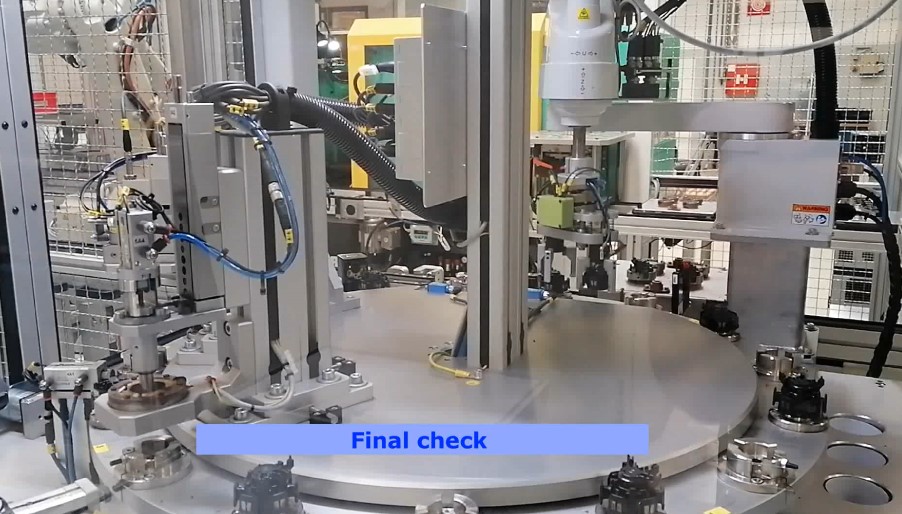
Pilot production line
Experiment Performance
During the Qu4lity project we have successfully further developed several key components of the Kolektor Digital Platform. SINAPRO.IIoT MES/MOM automatic data acquisition enables better process control – monitoring process stability and provides the possibility of in-depth analysis and search for important relationships between data. KiS enables users to develop, monitor and maintain machine vision quality control applications. With the KiS AI part of the platform, users can manage data and create powerful predictive models, which are more robust and can more easily detect defects in production.
The pilot production line has achieved:
- Overall Equipment Effectiveness (OEE), 10% Increase
- Parts Per Million (PPM), 20% Decrease
- First Pass Yield (FPY), 1% Increase
All successful steps enabled the company to improve Overall Equipment Effectiveness and reduce the scrap rate.
Value chain
Observations & Lessons learnt
Kolektor has been developing Kolektor Digital Platform, which is a proprietary digital platform that allow us to provide products and services for the factories of the future (FoF). An integral part of this platform are services that support intelligent IoT sensors, communications with other machines, devices, and services (including robots) and Big Data (based on AI).
Data driven or cognitive approaches in manufacturing optimization demand working with big data, which must be interpreted with vast domain knowledge and experience. Tools and methods that support data consistency and symmetry enable timely development of cognitive solutions. Digital twins and software platforms that support such approaches are a necessity. Successfully deployed solutions enable companies the reduction of scrap rates and increase in overall equipment effectiveness.
Replication Potential
The pilot is composed of several components. KiS was used for cognitive visual quality control of the product. Sinapro.IIoT was used in the project to capture data from production machines and devices. The pilot served as an environment for testing new communication protocols (OPC-UA, MQTT), basic processing of captured data, and different visualization approaches. CEA’s acoustic sensing was intended for the lathe knife wear detection. Autonomous visual quality control was supported by JSI’s robot supported visual quality control to achieve proper vantage points.
The pilot was the bedrock for the development of the components and a framework to evaluate all the integral parts. The technology is now being further developed as a product to monitor the production processes and the flow of the material in the factory to create a faithful digital twin. Such data can be used to optimize the production processes and achieve ZDM.
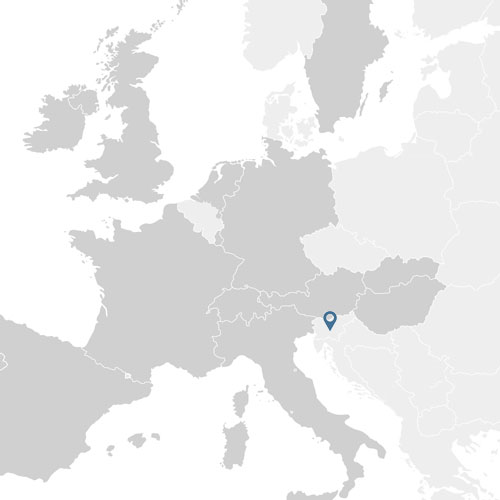
Kolektor, Slovenia
Pilot Partners
Standards used
- MQTT
- ROS
- GigE Vision
- ISO/TS 15066
- OPC UA
Digital Platforms & Tools
- KDP, KiS
- KDP, Sinapro.IIoT
- ReconCell
Big Data Characterization
Data types
- Sensor data
- Machine data
- Images
Number of sources
- Environmental / material parameters
- Machine parameters
- Operational data
Open data
No
Key Facts & KPIs
Productivity
PR1 – Overall Equipment Effectiveness improved for 10%
PR2 – Parts Per Million decreased 20% times
PR2 – First Pass Yield is 1%
Adoption Assessment
Technical feasibility
Economic feasibility
Replication potential