Integration of IDS in the Mondragon Process Pilot
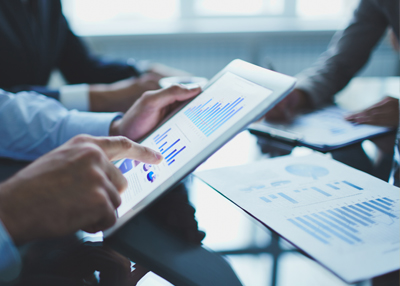
The Mondragon Process Pilot validates different technologies and standards with the goal to achieve zero defect and autonomous Quality in Machinery Building for Capital Goods sector involving two industrial scenarios: Manufacturing Processes with Cutting/Grinding Machinery for Railway (supported by Danobat) and Manufacturing Processes with Hot Stamping Machinery for Automotive (supported by Fagor Arrasate). The pilot requires to share data with 3rd party organisations for data analysis or anomaly detection. This must be achieved in a secure and control manner. International Data Space (IDS) connectors are used in the pilot to share process data between the pilot repository and the data service providers (data experts). Researchers from Fraunhofer institute and Mondragon Goi Eskola Politeknikoa (MGEP) have contributed to the deployment and implementation of the IDS connectors in the pilot.
MONDRAGON Corporation, Basque Country, Spain, is a very diversified worldwide group with around 82.000 workers in the areas of Industry, Knowledge, Retail and Finance. MONDRAGON as industry member of QU4LITY project Co-funded by the Horizon 2020 Under grant agreement No 825030 leads the Process Pilot: Zero Defect & Autonomous Quality in Machinery Building for Capital Goods sector involving two industrial scenarios: Manufacturing Processes with Cutting/Grinding Machinery for Railway, supported by Danobat and Manufacturing Processes with Hot Stamping Machinery for Automotive, supported by Fagor Arrasate.
With the aim of coping with ZDM objective and under digital transformation plan of the group, one of the major challenges of MONDRAGON process pilot is to agglutinate the aggregate datasets from heterogeneous industrial systems and different stages of the process from two different manufacturing lines stablishing a dashboard showing alerts and deviations thought the industrial process.
Additionally, the data collected is used to evaluate industrial processes. Performance is satisfactory when parameter values are within certain thresholds. Process data can be further analyzed to detect anomalies that impact on the result. For specific evaluation, 3rd party experts are required to analyze those data. Data agreements between the parties are necessary to negotiate the conditions for access and usage of the data.
In the pilot, an IDS platform deployed by Fraunhofer-ISST and MGEP assures that those data are used only by the companies specific in the agreements established in the contract. The objective is to demonstrate successful data sovereignty for critical production data to mitigate trust issues with partners external to the company
The architecture of the solution is shown in the figure. Data is shared using IDS connectors that collect the contracts agreed between the sites. The code used for the implementation of the IDS platform in the pilot is available at https://github.com/industrial-data-spacex.