How to repurpose a factory in a crisis
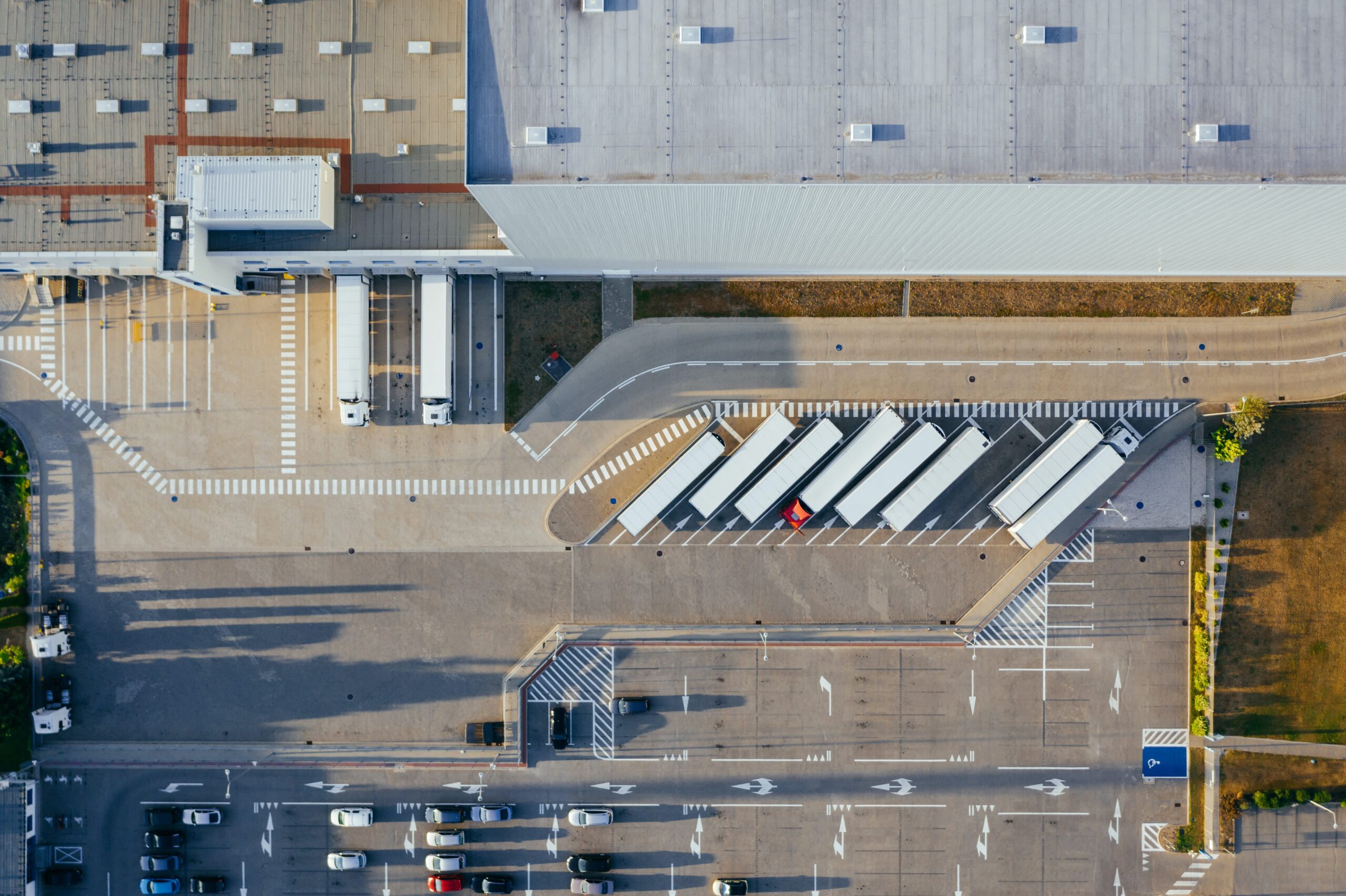
China accounted for 28% of manufacturing output before the pandemic. When China’s factories and borders closed, and transport routes were disrupted, the impact was global. At the same time, medical supply companies faced a rapid surge in demand.
Europe’s factories could not entirely make up for the shortfall, although some countries, including Italy and the Netherlands, turned to local networks of 3D printing companies to fill supply gaps at the start of the pandemic.
One vital way to keep supply chains working in a crisis is to repurpose local factories so they can fill gaps in supplies when demand soars or transport routes are disrupted, experts say.
‘Where we have existing (local 3D printing) networks it’s easier to start production, especially for less complex devices like face masks and glasses,’ said Angelo Marguglio, coordinator of the Eur3ka project, which was established in the wake of the pandemic to help Europe’s medical suppliers become more resilient to the next crisis.
The Eur3ka project wants to help small and medium-sized companies to be primed to repurpose their machinery to make a new product within 48 hours if another crisis hits.
Certification
One key challenge is certification. Even if a factory can rapidly repurpose its manufacturing processes, it cannot supply medical goods without authorisation from a medical authority. ‘You have to certify your machinery, your production process, your workforce skills, as well as the final product,’ said Marguglio, who is head of the Smart Industry and Agrifood R&D Unit at Engineering Group, an international company working on digital transformation. Eur3ka is working with medical authorising bodies to establish a pre-certification scheme for businesses, which can be rapidly turned into full certification when needed. ‘It’s a sort of pre-cooked certification process, so you can start production quickly,’ he said.
To obtain that pre-certification, companies need information on what changes to machinery, processes and staff skills are needed. And that requires the trust and collaboration of the company holding the patent for the product and process. ‘I, as the product owner, will only give you the licence to start producing my product if I trust you to use this IP-protected file or process within the terms we agreed – so only during the pandemic for example.’
Since the start of the pandemic, owners of some patented products and processes have established their own secure networks with manufacturers, on a one-to-one basis. ‘It took some time, but it worked,’ said Marguglio. ‘The question is: How can we ease this collaboration and speed up this phase?’ he added. One solution Eur3ka is working on is developing a community – the Digital Factory Alliance – that connects existing networks of healthcare and government agencies, ICT companies, manufacturing companies, and bodies like the World Economic Forum. ‘It is not just a technological push that can solve the issue, it is not only a political push that can solve the issue. We need a multi-actor approach,’ said Marguglio.

‘It is not just a technological push that can solve the issue, it is not only a political push that can solve the issue. We need a multi-actor approach.’
Angelo Marguglio, Head of Smart Industry and Agrifood R&D Unit, Engineering Group

Risk
Another important change is to ensure supply chains are designed using a risk-based approach, says Marguglio. ‘You should select your suppliers not only on the basis of financial cost, but also ask: “What are the risks of relying on one single supplier or country?” … (and) build, design and operate the supply chain in a more flexible way,’ he said.
Although another pandemic could occur at any time, the next crisis is more likely to be political, he says. ‘In South America today, for example in Brazil, you have a lot of instability that could explode at any moment and in any direction.’ Even a very localised crisis can impact suppliers. For example, Hong Kong’s anti-government protests in 2019 resulted in the temporary closure of the world’s busiest airport for air cargo. Other risks include political decisions to restrict exports, for example when India banned the export of paracetamol in March 2020 to protect its domestic supplies.
But discovering the risks inherent in a particular supply chain takes a lot of work, says Saskia Sardesai, an expert on medical supply chains and senior scientist at Germany’s Fraunhofer Institute for Material Flow and Logistics. One supply chain could, for example, have 70 suppliers in it dotted across the globe and each supplier may only exchange production data with the next company in the supply chain, says Sardesai. ‘Even the automotive industry – which is one of the most sophisticated in terms of logistics – struggled during the pandemic because they did not know who all their suppliers were or where they were based, she said.
She is working on CO-VERSATILE, a project developing tools to help European medical suppliers and other businesses prepare for the next crisis. The CO-VERSATILE project is developing an online portal – called Digital Technopole – which offers European manufacturers advice and simulation tools on how to adapt their factories and supply chains in a crisis. ‘We look at who can provide raw materials, how you set up the supply chain, and (provide) instructions on how to set up the production line,’ said Sardesai.
Digitalisation
Many supply chains cannot quickly respond to sudden changes in demand because they take weeks to order and transform the raw material into the finished product. Digitalising supply chain information is vital to help companies act quickly in a crisis, she says. Small and medium sized companies usually send out orders by email or fax, and enter information about supplies and suppliers manually into a company’s database, says Sardesai. Companies cannot adapt quickly unless they collaborate closely with their suppliers, know the issues they face, and can identify the main bottlenecks. ‘Once you know that, you can act,’ said Sardesai.
This post How to repurpose a factory in a crisis was originally published on Horizon: the EU Research & Innovation magazine | European Commission.