Fault Detection and Prediction Models
BENTELER Trial: Predictive Maintenance
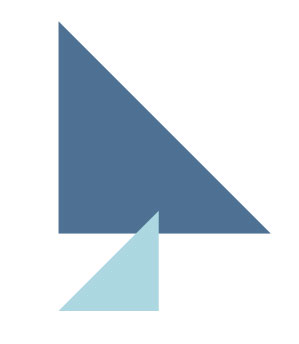
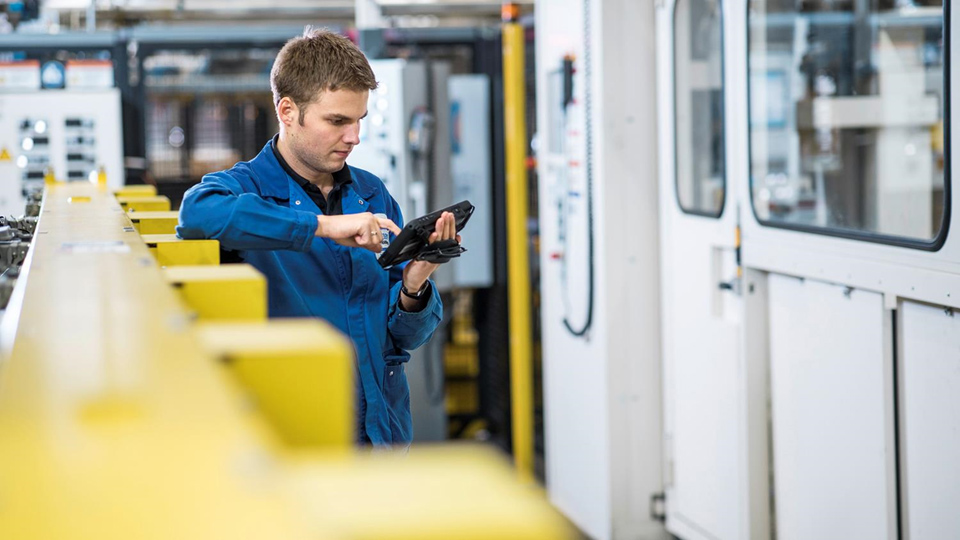
Data-Driven Digital Process Challenges
The complexity of the involved use cases along with the big volume of data, makes the Fault Detection and Prediction processes a challenging task. In addition, the Fusion of the results from different Fault Detection of Prediction approaches in order to provide a single result to the maintenance engineers without losing valuable information, adds-up to the complexity of the problem.
Big Data Business Process Value
The BENTELER Predictive Maintenance trial considers two main business processes for implementation which can be replicated in multiple production lines in different BENTELER plants:
Maintenance of a press system: This use case consists of a complex hot forming multistep fully automated process. The focus is the hot-forming press and more specifically the prediction of leakages in the hydraulic system of the press. Multiple sensors are installed on the press providing measurements with high frequency.
Maintenance of Scrap Belt: Multiple scrap or convey belts are utilized across all the BENTELER plants. The goal is to monitor sensorial input in order to detect problems in the functionality of the belt (e.g. scrap metal jammed under the belt).
To address both the business processes, a Predictive Maintenance platform has been developed, capable to handle the big volumes of data that are generated during the production process.
Large Scale Trial Performance Results
The BENTELER trial has enabled the development of a Predictive Maintenance Platform, which offers Fault Detection, Prediction and data analysis results Fusion capabilities to the maintenance department. The platform encapsulates software solutions from both the technology providers of the pilot providing a single output to the maintenance engineers.
The implemented data analysis solutions are capable of handling big volumes of data in a streaming of batch fashion, being able to utilize distributed data processing frameworks, like the Apache Flink or Apache Spark, respectively.
To make the most out of the Industry 4.0 technologies developed in the trials, BENTELER moved forward and implemented the Developers Space, a remote containerized environment on which multiple plants are connected mirroring their local data lakes with sensorial measurements from their production lines. This enables the application of the platform to a wider range of applications.
Observations & Lessons Learned
There are important lessons learnt in all the phases of the analysis of the use cases, starting from the communication between the domain experts, the data scientists and the developers, which is important in order to achieve the knowledge transfer for the domain understanding and the use case definition. Then the data infrastructure contributes significantly to the implementation and model transfer phases. A centralized infrastructure offering a containerized environment eases the development of a micro-service based predictive solution offering flexibility and easy distribution of the workload. Finally, the context awareness is important for the domain and data understanding, which in turn are important for the data modeling. However, the end solution should be context agnostic in order to be easily transferable to a wider range of use cases.
Replication Potential
The developed solution is replicable. The gathered experience from the expansion to a second BENTELER plant (i.e. Warbourg) will be utilized in the replication to the other plants. This has been possible because of the centralized infrastructure of BENTELER, which has been an own investment, and the seamless collaboration with the technology providers.
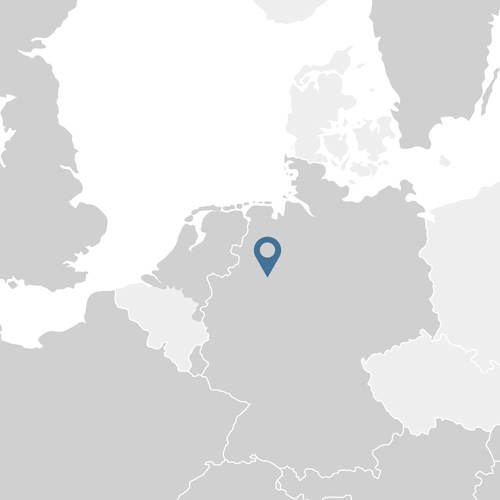
BENTELER Automotive Plant An der Talle
Paderborn | Germany
Pilot Partners
Standards used
- OPC UA
Big Data Platforms & Tools
- Flick
- Spark
- Kafka
Big Data Characterization
Data Volume
172TB
Data Velocity
23.6GB/day
Data types
- Sensorial Measurements
- Maintenance Logs
Number of sources
- Multiple sensors installed in both the hot forming press and the scrap belts.
- Maintenance logs from the engineers
Open data
No
Implementation Assessment
Technical feasibility
The technical solutions developed in the BOOST4.0 project were fairly easy to deploy at the pilot side. Especially after the completion of the first part of the experimentation, it was feasible to quickly deploy any updates and/or improvements.
Economic feasibility
It would be feasible to maintain and take advantage of the technical solutions developed in the BOOST4.0 project from the economic point of view, taking into consideration the added value. Specific agreements could be discussed.
Replication potential
The implemented predictive solution and the maintenance dashboards have been transferred to multiple sites, thus leveraging the benefit for BENTELER even further.