Danobat
Digital Machine for zero-defects at high precision cutting/grinding.
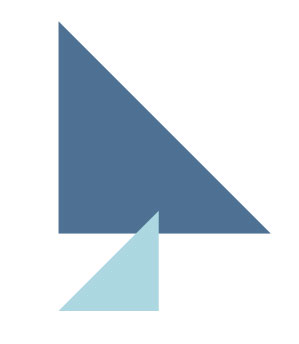
Danobat is a benchmark manufacturer of high value-added solutions in the field of grinding, turning, punching and bending. Danobat develops, in close collaboration with its customers, turnkey solutions for specific applications in the following sectors: aerospace, railway, automotive, energy, oil and gas, and metal forming. Danobat has been working in the last 6 years in the development of a digital strategy to provide solutions that add value to the client based on data from the machines.
Process Challenges
New business models are coming to the machine tool sector. Servitization is a term that has been used in the manufacturing sector for a long time, pay-per-use is starting to spread from just a few industries, like electricity or phones, to more traditional sectors. The technologies of IoT and Industry 4.0 paradigms are setting a technological basis for these new business models development.
Machine tool contracts have been including for several year OEE commitments from the manufacturer. Recently, some end users have also started thinking on pay-per-use contracts when buying a machine. The machine tool manufacturer has then to ensure not only availability but also productivity (so quality).
Historically, machine tool manufacturers have not had any information of the machine behaviour once they were working at the customer facilities. Maintenance actions by the machine tool supplier, where started by a customer’s call and where mainly related to corrective actions, once the failure had already happened.
Process Value
The aim of the project is to develop a more flexible, intelligent and autonomous system
The new architecture of the system to developed is a hybrid edge+ cloud system. The cloud infrastructure enables big data collection and real time information, shared between Danobat and customers. The analytics knowledge is developed in the cloud where there are no limitations to processing or storing capacity. The algorithms developed and tested in the cloud can be installed on the Edge system. Real time analysis of these applied algorithms triggers alarms to the machine, that can also be sent to the cloud. This system is less depending on a cloud connection. These warnings can activate actions on the machine, send information to the operator who can take decisions or can recommend maintenance actions with DANOBAT to avoid failures.
The system works in a closed loop so that the application of this knowledge on the machine can also generate new use cases that the domain expert can use and analyse to generate new smart functionalities.
This system is then the tool to observe the production process in real-time and to react to any circumstance during the process, advanced process control or real-time error corrections. Processes can therefore be optimized and product quality improved. Using real-time problem-solving, which reduces waste and production time.
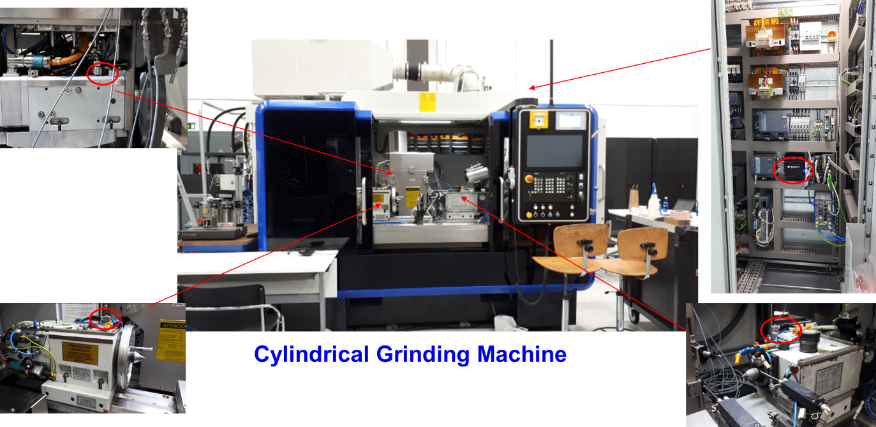
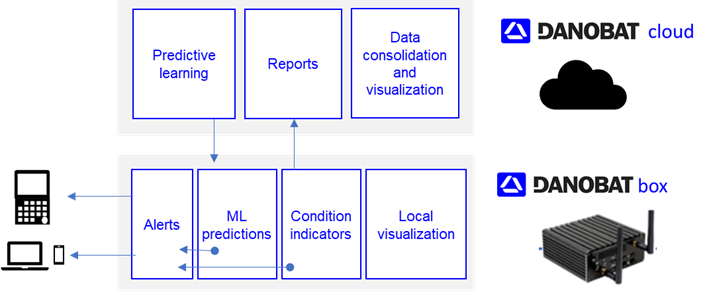
Experiment Performance
A general architecture was designed for the IT solution that supports all the developments that are being deployed in the QU4LITY project.
As a result of the deployment of the architecture, information about test conditions and continuous behaviour of the machine was gathered.
This information was analysed by experts leading to diagnosis of different issues on the machine components. It was also used to train algorithms by Atlantis.
The estimation of the RUL in Product Cycles (PCs) of the Z2 axis of the regulating wheel of the Danobat grinding machine was done. It was done through the utilization of the Neural Networks algorithm Long Short-Term Memory (LSTM).
Value chain
Observations & Lessons learnt
Working methods must be adapted to users of Operational technologies instead of Information technologies. Give also importance to training .
Replication Potential
This system is the tool to observe the production process in real-time and to react to any circumstance during the process, advanced process control or real-time error corrections. Processes can therefore be optimized and product quality improved. Using real-time problem-solving, which reduces waste and production time.
Digitalization and advanced analytics also enable the creation of digital replicas of physical assets. This is what we call a digital twin; a virtual model of a physical asset such as a machine on the shop. Digital twins of products, such as machine tools, can be used by manufacturers to analyse the actual product behaviour in relation to its original design. This allows us to recognize any behaviour deviations.
.
We sell digital solutions and digitalized machines to improve the life and efficiency of our machines. Quality has allowed us to take a significant step forward in our products and services.
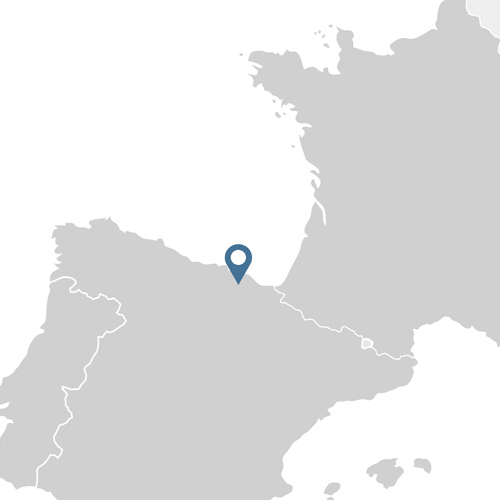
Danobat – Guipúzcoa, Spain
Pilot Partners
Standards used
- OPC_UA
- json
Digital Platforms & Tools
- Danobat Data System
- Atlantis Secision Support System
Big Data Characterization
Data types
- CNC
- PLC
- Controller
- Analysis results
Number of sources
- 4
Open data
No
Key Facts & KPIs
Productivity
PR1 – Machine availability increase 3%
PR2 – Life of key components 40%
Adoption Assessment
Technical feasibility
Economic feasibility
Replication potential