AUTOHARD
Piloting the Integration of BME Quality Data for In-line Autonomous Optimisation of Camshaft Hardening Processes Control
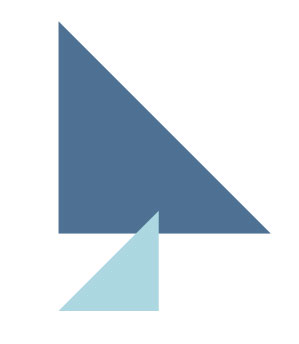
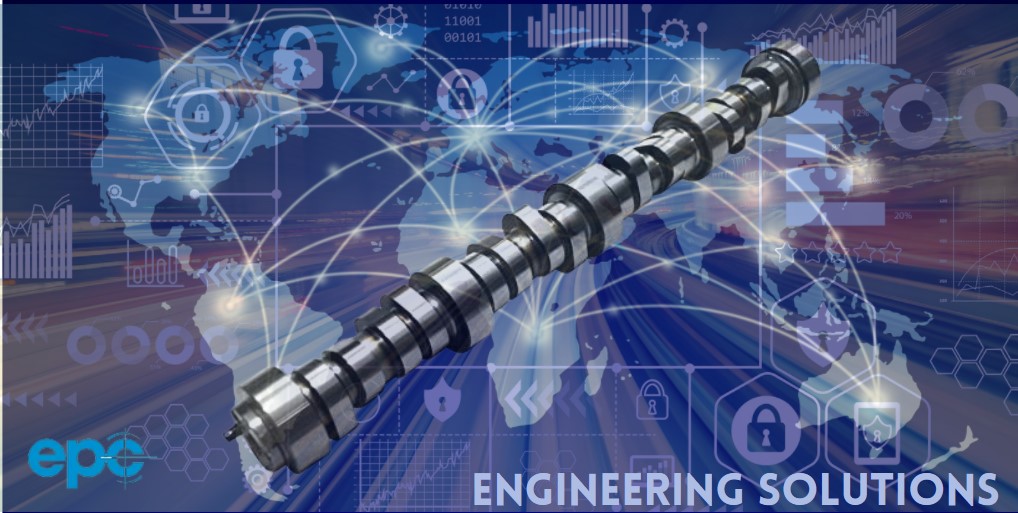
Components (EPC) focuses its activity on the manufacture of automotive parts, particularly camshafts, connecting rods and balance shafts, being one of the world’s leading manufacturers of camshafts for high-power engines (between 1- 10MW) diesel and gas for the power generation, naval and industrial sectors. The constant demand for efficient combustion engines that allow reducing fuel consumption in these sectors has made necessary new designs for large camshafts that reduce consumption and the weight of the engine, withstanding higher stresses through induction hardened surfaces, and the certification of its mechanical properties with advanced non-destructive techniques such as Barkhausen (BME).
Data-Driven Digital Process Challenges
The relevance of inspection technologies for EPC is undeniable. These techniques are a cornerstone of highly automated and competitive manufacturing processes with maximum precision, productivity, quality and reliability. For this particular case, characterized by high-demanding final application, big camshafts and complex process, the need for leading in-line autonomous control based on inspection and measurement solutions integration is a critical parameter for industry competitiveness. .
Big Data Business Process Value
By adopting a zero defects manufacturing and digitization (ZDM) strategy, EPC sets itself the goal of providing high added value, quality, robustness and low cost and environmental impact camshafts, not only for the automotive sector, but also for critical engine applications in the energy, marine, industrial, agricultural, mining or construction sectors.
EPC has detected the opportunity to automate the induction hardening stage control for its optimisation (in terms of quality, time, costs and efficiency). Thus, EPC aims at reaching a higher autonomous level (Production Level 4 following Qu4lity criteria) by correlating BME results and induction hardening machine parameters (set-up & real-time).
Large Scale Trial Performance Results
EPC obtains a new autonomous induction hardening control module that will be integrated into the large camshaft manufacturing line for application in the power generation, naval and industrial sectors.
It is important to mention that until now there was no commercial system that was capable of exploiting the knowledge obtained from the BME inspection of surface hardness, correlating its analysis with the process parameters and the status of the tempering operation. With the development of AUTOHARD, EPC will be able to measure and save all the data regarding the product quality. This offers the opportunity to meet the customer requirements in a more efficient way with a more reliable process, positioning the company as one of the camshaft manufacturing leaders in Europe.
Value chain
Observations & Lessons Learned
For EPC, this project represents a step forward in its desire to offer new and better products to the industry. Through the digitalization of its processes EPC is able to provide high added value camshafts with high quality but with low cost and environmental impact.
The next steps are focused on generating the services regarding the analysis of rules and prediction results coming from QARMA classifier to automatically optimise the induction hardening process.
Replication Potential
AUTOHARD was developed to control the induction tempering process of large camshafts in an autonomous way. The module helped EPC progress on their way to zero defect manufacturing. The implementation of the Qarma enabler is a step forward on the deployment of a quality framework that integrates the online quality controls with the workflow solutions.
“AUTOHARD is a step forward on the quality strategy for camshafts manufacture”
The development of AUTOHARD helped in the collection of information related to the induction hardening process. Until know there was not a commercial software that allowed the intercorrelation of the heat treatment parameters with the hardness results. This improvement compared to the competitors will push EPC achieving a best position in the market of big camshaft manufacture.
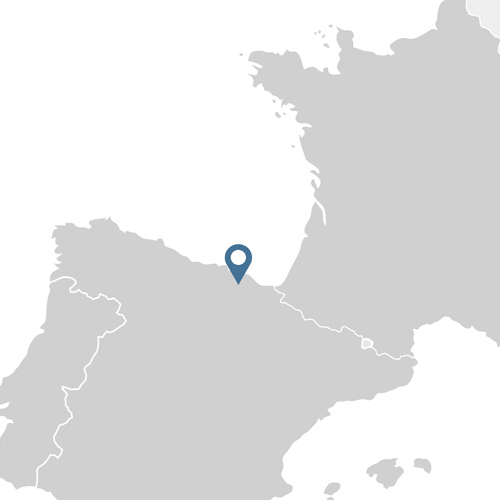
EPC Group Europe, Eibar, Gipuzkoa, Spain
Pilot Partners
Big Data Characterization
Data types
- CSV
- Txt
Number of sources
- BME Hardness Inspection machine
- Induction Hardening station
Open data
No
Key Facts & KPIs
Productivity
PR1 – Inspection time reduction 50%
PR2 – Product cost reduction 40%
P33 – Nonconformities in client reduction 40%
Sustainability
SU1 –Waste and material reduction 50%
Agility
AG1 – Lead time reduction 20%
AG2 – Process set-up time reduction 50%
Adoption Assessment
Technical feasibility
Economic feasibility
Replication potential