De- and Re-manufacturing of consumer WEEE

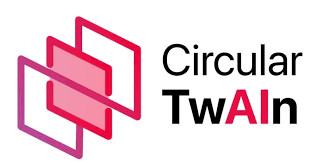

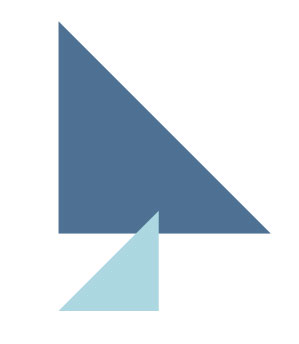
General Information
Challenge, Value & Description
Performance, Access & Contact
1 – General Information
Partners



Sectors addressed
- electric_engineering
- electronics_electrical
- environmental_green
- ict
Application categories covered
https://www.circular-twain-project.eu/use-cases
Geographical Scope
- Europe
Lifecycle level covered
Smart Maintenance
Customer Service
Circularity
2 – Challenge, Value & Description
Challenge
Prior to the WEEE Pilot, the management of electronic waste was inefficient, labour-intensive, and environmentally unsustainable. Manual sorting and disassembly processes were slow and prone to errors, leading to low recovery rates of valuable components and materials. The lack of real-time data and traceability hindered effective decision-making and compliance with environmental regulations. Stakeholders operated in silos, with limited data exchange and coordination. As a result, many reusable parts were discarded, hazardous materials were mishandled, and the overall process lacked transparency, scalability, and economic viability—posing a significant barrier to achieving circular economy goals.
Value
Following the implementation of the WEEE Pilot, the management of electronic waste became significantly more efficient, traceable, and sustainable. AI-powered recognition systems and robotic disassembly reduced manual labor and increased the speed and accuracy of component sorting. Real-time data sharing through a federated dataspace enabled seamless coordination among stakeholders, improving compliance and decision-making. Valuable components were identified and recovered more effectively, reducing environmental impact and increasing economic returns. The integration of digital twins and predictive analytics further optimized operations, transforming WEEE processing into a scalable, data-driven circular model.
Description
The WEEE Pilot establishes a seamless, traceable data exchange process across the entire electronic waste value chain—enabling collaboration, regulatory compliance, and circular economy practices through a federated dataspace and Digital Product Passport (DPP).
The process begins with a producer or OEM registering a product, uploading key technical specifications and component-level data into the dataspace. This data is linked to a Digital Product Passport—a persistent digital identity that follows the product throughout its lifecycle.
At end-of-life, collection centers log the device’s arrival, recording its condition, type, origin, and any potential hazards. This information is updated in the dataspace and accessed by authorized dismantlers. Using AI-assisted tools and robotic systems, dismantlers identify, sort, and disassemble components, documenting each action: what is removed, what is reusable, and what is routed for recycling. These insights are continuously fed back into the DPP.
Testing facilities may evaluate specific components for reuse, uploading diagnostics and performance data. If components meet quality standards, remanufacturers access the data to integrate them into new products, updating the DPP with the new configuration and extended lifecycle.
Recyclers then retrieve material composition data to optimize recovery processes. They report recovery rates, hazardous material handling, and environmental impact, further enriching the dataspace.
Throughout the entire process, secure, role-based access ensures that each actor sees only what is relevant to their role. Meanwhile, the Digital Product Passport provides a transparent, auditable record of the product’s journey—enabling informed decisions, efficient resource use, and a more circular approach to managing electronic waste.
Infraestructure Elements
- Private Cloud
3 – Performance, Access & Contact Info
Performance
In the WEEE Pilot, the Circular TwAIn project tackled the inefficiencies and environmental challenges of electronic waste management by introducing a data-driven, AI-enhanced, and collaborative approach. Previously, the process was largely manual and fragmented. Devices were collected and dismantled with limited information about their composition or condition, leading to low recovery rates, safety risks, and the unnecessary disposal of reusable components.
To address this, the pilot introduced a combination of AI-powered recognition systems, robotic disassembly, and a federated dataspace integrated with Digital Product Passports (DPPs). These technologies enabled stakeholders—producers, collection centers, dismantlers, testing facilities, remanufacturers, and recyclers—to share and access real-time data about each product’s lifecycle, condition, and material composition.
As a result, disassembly became faster, safer, and more precise. Valuable components were identified and recovered more effectively, while hazardous materials were handled with greater care. The dataspace ensured secure, role-based access to information, improving coordination and compliance across the value chain.
The main benefits include:
- Increased recovery and reuse rates
- Reduced environmental impact
- Lower operational costs through automation
- Improved traceability and regulatory compliance
- Enhanced collaboration among stakeholders
This pilot demonstrated how digitalization and AI can transform WEEE management into a scalable, circular, and economically viable system.
Lessons Learned & Observations
The WEEE Pilot offered valuable insights into the challenges and opportunities of applying digital and AI technologies to electronic waste management. One of the most important lessons learned was the need for standardized, high-quality data. Many devices entering the waste stream lacked consistent documentation, making it difficult to automate disassembly or assess component value. This highlighted the importance of early data integration—starting from product design and manufacturing—and the role of the Digital Product Passport (DPP) in ensuring traceability.
Another key takeaway was the importance of stakeholder collaboration. The pilot showed that circularity cannot be achieved in isolation. Effective data exchange through a federated dataspace enabled dismantlers, recyclers, and remanufacturers to make better decisions, but it also required trust, governance, and clear access rules. Building this ecosystem was as much a social and organizational challenge as a technical one.
The use of AI and robotics proved highly beneficial, but also revealed the need for flexible systems that can adapt to the wide variety of WEEE products. Training AI models to recognize and handle diverse devices required large, well-labeled datasets—something that future pilots should prioritize from the start.
Finally, the pilot confirmed that digitalization can unlock both environmental and economic value. By improving recovery rates, reducing manual labor, and enabling reuse, the WEEE Pilot demonstrated a viable path toward a more circular and sustainable electronics industry.
Replication Potential & Feasibility Assessment
The WEEE Pilot has demonstrated strong potential for replication across different regions and types of electronic waste streams. Its modular and interoperable architecture—built around AI, robotics, a federated dataspace, and Digital Product Passports (DPPs)—makes it adaptable to various operational contexts, from small dismantling centers to large-scale industrial facilities.
From a technical standpoint, the pilot is highly feasible to replicate. The technologies used, such as AI-based recognition systems and robotic disassembly, are mature and can be integrated with existing infrastructure. The use of open standards and APIs ensures interoperability, while the dataspace model supports secure, role-based data sharing across diverse stakeholders.
Economically, the pilot has shown that digitalization can reduce operational costs by automating labor-intensive tasks and improving material recovery rates. The ability to identify reusable components and optimize recycling processes increases the value extracted from each device. Moreover, the system supports compliance with evolving EU regulations, such as the Ecodesign and Waste Framework Directives, which is increasingly important for producers and recyclers.
In summary, the WEEE Pilot offers a scalable, technically robust, and economically viable model for transforming electronic waste management into a circular, data-driven process. Its replication could accelerate the transition to a more sustainable electronics industry across Europe and beyond.